Battery shortage halts Audi e-tron production
25 February 2020
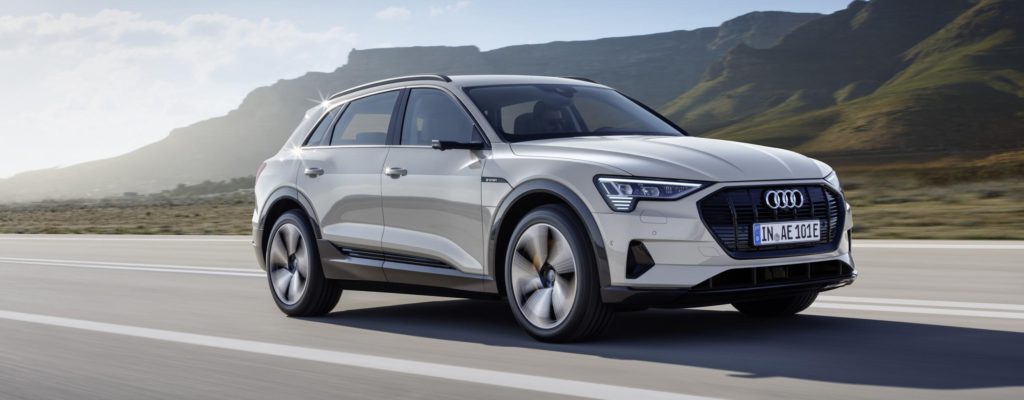
25 February 2020
Audi paused the production of its e-tron electric SUV on 20 February but is due to resume manufacturing today (25 February). The move came as the carmaker addressed the need to resolve production issues, including bottlenecks in battery supply.
This is unwelcome news for the German manufacturer given their plans to expand the e-tron range. A Sportback version with a coupe-style declining roofline has recently been launched and a performance sedan, the e-tron GT, is expected too.
LG Chem usually supplies the batteries for the electric vehicle (EV). However, German media reports suggest shortages at LG Chem’s Poland factory are the reason behind the delays. Plans were in place to build 80,000 e-trons this year but LG can only provide 40,000 battery cells, according to the business paper Handelsblatt. As the battery specialist is Audi’s only cell supplier, the carmaker is looking for supplies from alternative battery companies the paper said.
Bumpy road
While Audi reportedly sold about 26,400 e-trons last year, this progress hasn’t come without bumps in the road. The car’s market launch was delayed after its unveiling in September 2018. Then, in 2019, deliveries were delayed again because of battery-supply issues. The Brussels Times reported waiting times were expected to treble from two months to between six and seven months.
Last year Audi issued a recall for the e-tron after discovering a potential risk of battery fire. Roughly 7,000 vehicles were thought to be affected, including 2,300 in Germany. Audi said that moisture could get into the electrical system under certain circumstances, meaning a possible electrical short and then a potential fire.
Electric investment
These supply issues come on the back of increased pressure on carmakers to invest in electrification and digitisation programmes.
Last year Volkswagen (VW) Group pledged to invest €60 billion on hybridisation, electric mobility and digitisation over the next five years. This amounts to slightly more than 40% of the group’s investment in property, plant and equipment alongside research and development costs. Just over half of this budget, €33 billion, has been earmarked for electric mobility.
′We will step up the pace again in the coming years with our investments. Hybridisation, electrification and digitalisation of our fleet are becoming an increasingly important area of focus. We intend to take advantage of economies of scale and achieve maximum synergies. In light of the worsening economic situation, we are also working on increasing our productivity, our efficiency and our cost base to secure meeting our targets,’ Herbert Diess, CEO of the Volkswagen Group said in November last year.
Daimler is also changing its organisational structure to meet the demands of the electrified market. The carmaker is set to cut 10,000 jobs worldwide, including managerial positions, in order to increase electric and digital investment.
′At Daimler, we are working hard to achieve our major strategic goals: The gradual switch to CO2-neutral mobility and the full use of digitalisation for products and processes’ said chairman Ola Källenius.
With mounting stakes and swelling investments in electric and alternative-fuel solutions, manufacturers face a growing conundrum. Will it be possible to meet the growing demand for EVs, bolstered by stricter emissions targets, with battery manufacturers struggling to keep up?