BMW develops sustainable material cycle for batteries
31 July 2020
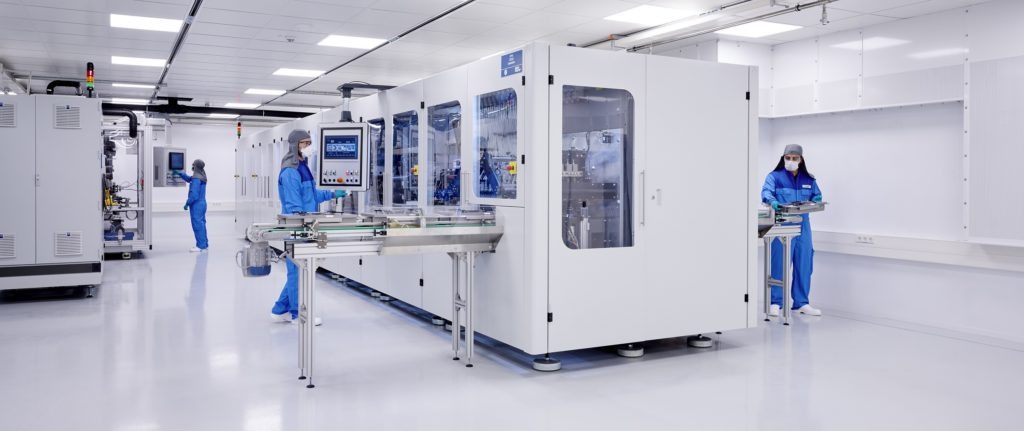
31 July 2020
BMW Group is creating a closed and sustainable material cycle for battery cells. The move plays into the carmaker’s belief that sustainability is central to the expansion of electromobility.
A pilot lithium-ion battery cell plant will be built in Parsdorf, near Munich, and is scheduled to commence operations in late 2022. Roughly 50 employees will work at the facility, which has a total project volume of almost €110 million.
BMW wants to penetrate all aspects of the battery-cell value chain with the new plant. This will include material selection, battery-cell composition and design, as well as near-standard production and recycling.
Electrified expertise
In November last year, the carmaker opened a separate battery-cell competence centre in Munich. The objective is to cover the entire value chain, from research and development to composition and design, all the way to large-scale manufacturability.
By opening its new pilot plant in Parsdorf, the group plans to enhance the performance of its battery cells and demonstrate large-scale manufacturing capabilities. This means developing innovative production processes, which will then be installed at the new 14,000 square metre location.
BMW wants to use production processes also employed in standard production, hoping to demonstrate the industrial feasibility of future battery-cell generations. The primary focus will be on optimising production efficiency, costs and quality.
′The new pilot plant will strengthen our expertise in the production of battery cells,’ said Milan Nedeljković, member of the board of management responsible for production. ′We will be capable of testing new systems technology and innovative production processes.’
He claimed the new plant will make BMW the first manufacturer to cover the entire process chain for electric vehicles (EVs). ′The new pilot plant will enable us to close the final gap in the value chain from battery cell development, to production of modules and powertrain components, all the way to installation of fully assembled high-voltage batteries at our vehicle plants,’ Nedeljković said.
Entire value chain
′By 2023, the BMW Group will have 25 electrified models on the roads, as it systematically increases electrification across all brands and model series,’ Frank Weber, member of the board of management responsible for development said. ′This continued expansion and our comprehensive battery-cell expertise will give sustainability a major boost.’
Weber explained the carmaker is not solely focused on the most efficient battery cell, but its entire value chain. ′That is why we are working with our partners to create a closed material cycle for battery cells,’ he said.
BMW has already reached an agreement with its manufacturers that they will only use green power to produce fifth-generation battery cells. These will be used in the BMW iX3, which is due to hit the roads later this year. The upcoming iNEXT and the i4 also look to benefit from these batteries.
Sustainable batteries
EVs produce a third less CO2 across their lifetime (including production) than internal combustion engines. But BMW points out that up to 40% of a fully-electric vehicle’s CO2 emissions still comes from battery-cell production alone. Therefore, to contribute to climate protection, the manufacturer wants to improve this energy-intensive process.
To develop more sustainable technology, the carmaker is working as part of a consortium with battery manufacturer Northvolt and developer of battery materials, Umicore. They are looking to create an end-to-end sustainable value chain for battery cells in Europe, extending from development to production and then recycling.
Northvolt will produce cells at its gigafactory currently under construction in Skellefteå in northern Sweden from 2024. Meanwhile, Umicore will contribute to the development of a sustainable battery in Europe. Recyclable cell design is now a consistent focus from the very beginning of development.
In June, Northvolt also formed a joint venture with Norsk Hydro, to enable the recycling of battery materials from the Norwegian EV market. The new venture, Hydro Volt, will establish a recycling hub in Norway, which will begin operations in 2021.
Elsewhere, Honda and battery manufacturer Contemporary Amperex Technology (CATL) announced they will form an EV battery alliance. Their discussions will revolve around joint development, stable supply and the recycling and reuse of EV batteries.