Daimler begins work on new gigafactory to build EU supply chain
23 May 2017
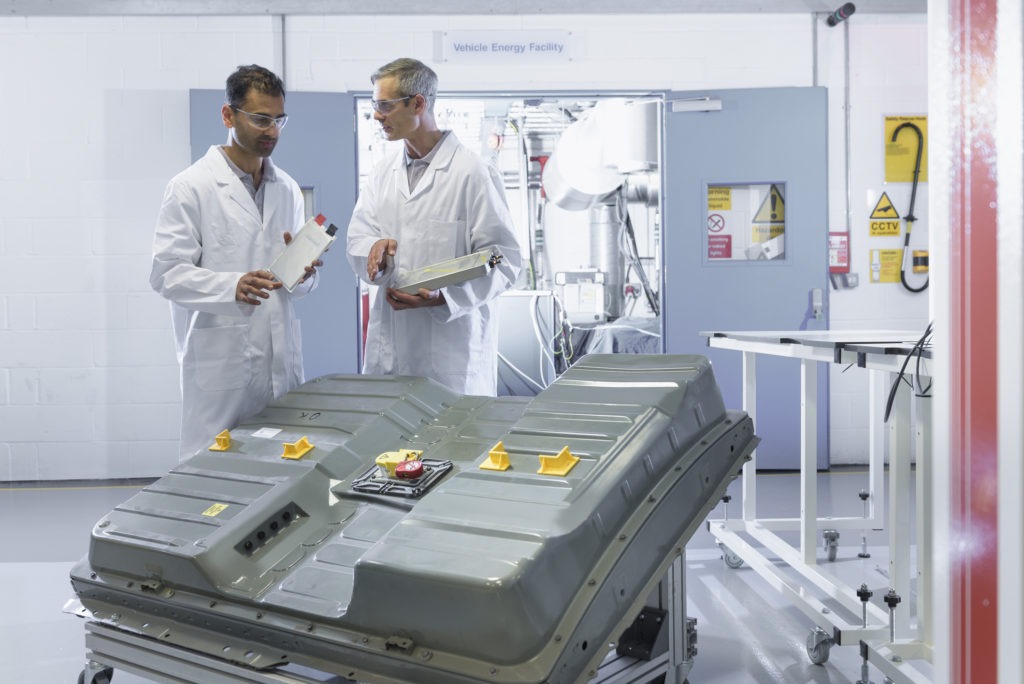
23 May 2017
With European vehicle manufacturers looking for their electric vehicle (EV) models to achieve total cost of ownership (TCO) parity with petrol engine cars, there needs to be a strong supply chain for specialised components within the continent itself.
The vehicle supply chain adds to the cost of a model when it is developed and brought to the showroom. The ability to build components close to the production facility, and in greater numbers, ultimately lowers the cost of components. For EVs, this lower cost can be translated into a reduction in the price of the vehicle, as well as an increase in the number of models.
While both BMW and Audi have announced plans to increase their range of EVs, Daimler has taken a further step towards an integrated supply chain, by beginning the construction of a €500 million plant near Berlin, Germany, which will assemble lithium ion units for its models. The ′gigafactory’ is seen as aiding a quicker shift towards green power for both vehicles and utilities.
The factory will be the second production facility for batteries owned by Daimler, however it will also be significantly bigger at around 20 hectares. It is hoped that the facility could pose as a rival to Tesla’s production plant in Nevada which is currently under construction to aid the demand for the company’s new Model 3.
Speaking at an event to mark the beginning of construction, Dieter Zetsche, chairman of the board of Daimler AG and head of Mercedes-Benz Cars, commented: ′The automotive industry is facing a fundamental transformation and we see ourselves as the driving force behind this change. The battery factory in Kamenz is an important component in the implementation of our electric offensive. By 2022, we will have more than ten purely electric passenger cars in series. We also continue to drive forward the hybridization of our fleet. Under the EQ brand, we are creating a holistic ecosystem for e-mobility.’
Currently, electronics makers in Asia hold the largest share of the lithium ion battery business, and this is expected to be maintained with eight further large manufacturing facilities being built in China. This means that batteries for vehicles require shipping into production facilities in Europe, which adds cost when purchasing and logistics are taken into account. The production of batteries in Europe could lessen this.
Nikolas Soulopoulos, an analyst with the London-based research arm of Bloomberg LP, comments: ′As battery costs fall and their energy density increases, we could see cheaper battery-electric cars than their fuel-burning equivalents by 2030.’
As well as batteries for vehicles, the new Daimler plant will produce units for energy storage. Boris von Bormann, chief executive officer of Mercedes-Benz Energy Americas, adds: ′Looking a few years out, as we have a stronger penetration of EVs in the market, you’ll have more demand on the grid, which may need to be supported by storage.’
Large-scale factories planned in Sweden, Hungary and Poland, as well as Daimler’s battery assembly plant in Germany, are expected to feed demand from automakers such as Volkswagen Group and Renault. This could help to cut the cost of lithium ion packs by 43%, which would make EVs a much more acceptable price to everyday consumers. The development of such plants in Europe highlights vehicle makers’ commitments to rolling out more EVs and concentrating on low and zero-emission vehicles.