Making automotive manufacturing more sustainable
25 March 2021
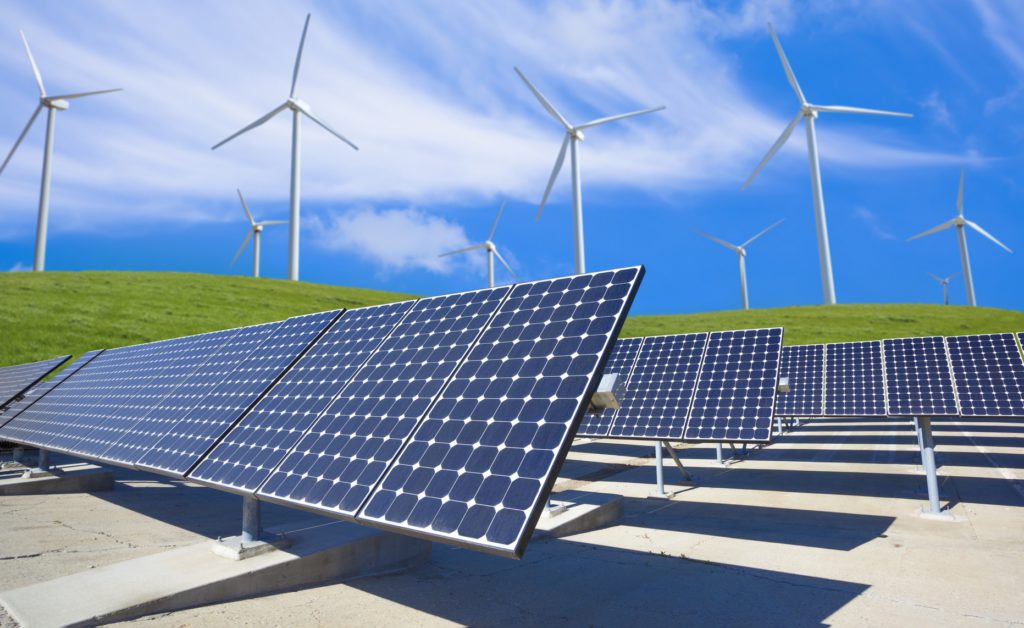
The transition to climate-friendly transport means new electric and low-emission drivetrains. But what about the factories these vehicles roll out of? The likes of battery-electric vehicles (BEVs) and plug-in hybrid-electric vehicles (PHEVs) will seem like an empty gesture unless OEMs can provide green credentials for their production lines.
A couple of notable examples include Volvo Cars and Audi. The Swedish carmaker recently confirmed its Daqing plant in China is powered by 100% climate-neutral electricity. Meanwhile, Audi is looking to reduce CO2 emissions during component production, taking aim at the e-tron GT’s wheels. Volkswagen Group’s luxury car brand is also examining its water consumption, planning to implement closed-water cycles in the long term.
A powerful landmark
Volvo’s Daqing plant is now powered exclusively by climate-neutral electricity. The site follows in the footsteps of its Chengdu factory, which reached the same milestone last year. The Daqing plant will now be reliant on biomass (83%) and wind power (17%), with an estimated annual CO2 emissions reduction of roughly 34,000 tonnes
Ensuring the power generator’s green credentials meet expected climate-friendly standards, Volvo revealed the biomass power plants use locally and sustainably-sourced agricultural and forestry residues. ′For us at Volvo Cars, sustainability is as important as safety,’ said Javier Varela, senior vice president for industrial operations and quality. ′To achieve our ambitious climate targets, tackling emissions from our manufacturing network is crucial, and I am very pleased that Daqing is now powered by 100% climate-neutral electricity.’
Globally, the carmaker’s manufacturing network is now powered by nearly 90% climate-neutral electricity. Looking ahead, Volvo hopes to make its manufacturing operations climate-neutral by 2025. To reach this goal, the carmaker will need to access climate-neutral electricity and heating. This means finding local partners in government and business that support sustainability.
′We can only achieve our climate action targets by working together with our suppliers,’ said Varela. ′We are encouraged by the support we have received so far in China and aim to be a benchmark of sustainability for its manufacturing industry.’ More broadly, Volvo wants to be a completely electric car brand by 2030 and a climate-neutral company by 2040.
Wheely green aluminium
As part of a pilot project for the e-tron GT, Audi will source optional 20-inch wheels made from low-CO2 emission aluminium supplied by Alcoa to the part’s manufacturer, Ronal Group. To achieve this, the metal goes through a smelting process that emits oxygen instead of carbon dioxide.
This approach is being further developed by the joint venture, Elysis. The venture’s smelting technology causes no direct CO2 emissions when compared to the traditional process used to make aluminium. This is thanks to an ′inert anode’ that replaces the carbon ones traditionally used in electrolysis, through which primary aluminium is made.
Alcoa is supplying Ronal with a blend of metal from the Elysis process and Alcoa’s low-carbon aluminium. Produced using flow-forming technology for weight optimisation, the wheel’s propeller-design improves aerodynamics. The mounted blades are roughly three millimetres thick, largely covering the wheels and helping aerodynamic efficiency. Audi first began a programme to lower CO2 emission in its supply chain in 2018.
′Aluminium is the focus of our CO2 programme because producing this material requires a high-energy input. The aluminium has already caused major CO2 emissions in upstream processes before it even arrives at Audi. We are therefore actively searching for innovative processes that help reduce CO2 emissions as early as possible in the creation process. The process created by Elysis is promising because it already takes effect in the raw material processing phase,’ said Marco Philippi, head of procurement strategy. ′These kinds of innovations allow us to increase our sustainability performance in the supply chain and ensure that our models arrive at the customers with a smaller carbon footprint.’
′Closed-water cycle’
Audi is looking at keeping its water consumption to a minimum as well as removing drinking water from vehicle production in the future. It is implementing closed-water cycles and increasing the use of rainwater. In the long term, the company hopes to use these systems at all of its production locations.
Source: Audi
′Our aim is to drastically reduce our freshwater consumption and cut the water consumption per produced vehicle in half by 2035,’ said Peter Kössler, board member for production and logistics. ′Where possible, we are already using recycled water that has been used multiple times in the cycle and treated. Our vision is to have closed water cycles at all our production sites.’
Audi uses a site-specific water value, withdrawing in relation to regional availability. Taking the local area into account means the carmaker considers areas where water is particularly valuable. This means water consumption can be reduced from the current average of around 3.75 cubic meters to some 1.75 cubic meters per car by 2035.
Audi also uses rainwater basins at multiple sites to help cover demand. For example, Audi México utilises a reservoir with a capacity of 240,000 cubic meters, which fills up in the six-month rainy season. The use of rainwater is to be increased at other locations over the next few years.
Lowering environmental impact not only in terms of CO2 emitted by a car, but also by the factory it was made in and the materials used to make it will help bolster these OEMs’ green credentials. BEVs and PHEVs will not be enough to see carmakers through the transition to a climate-friendly future, a holistic approach is key.
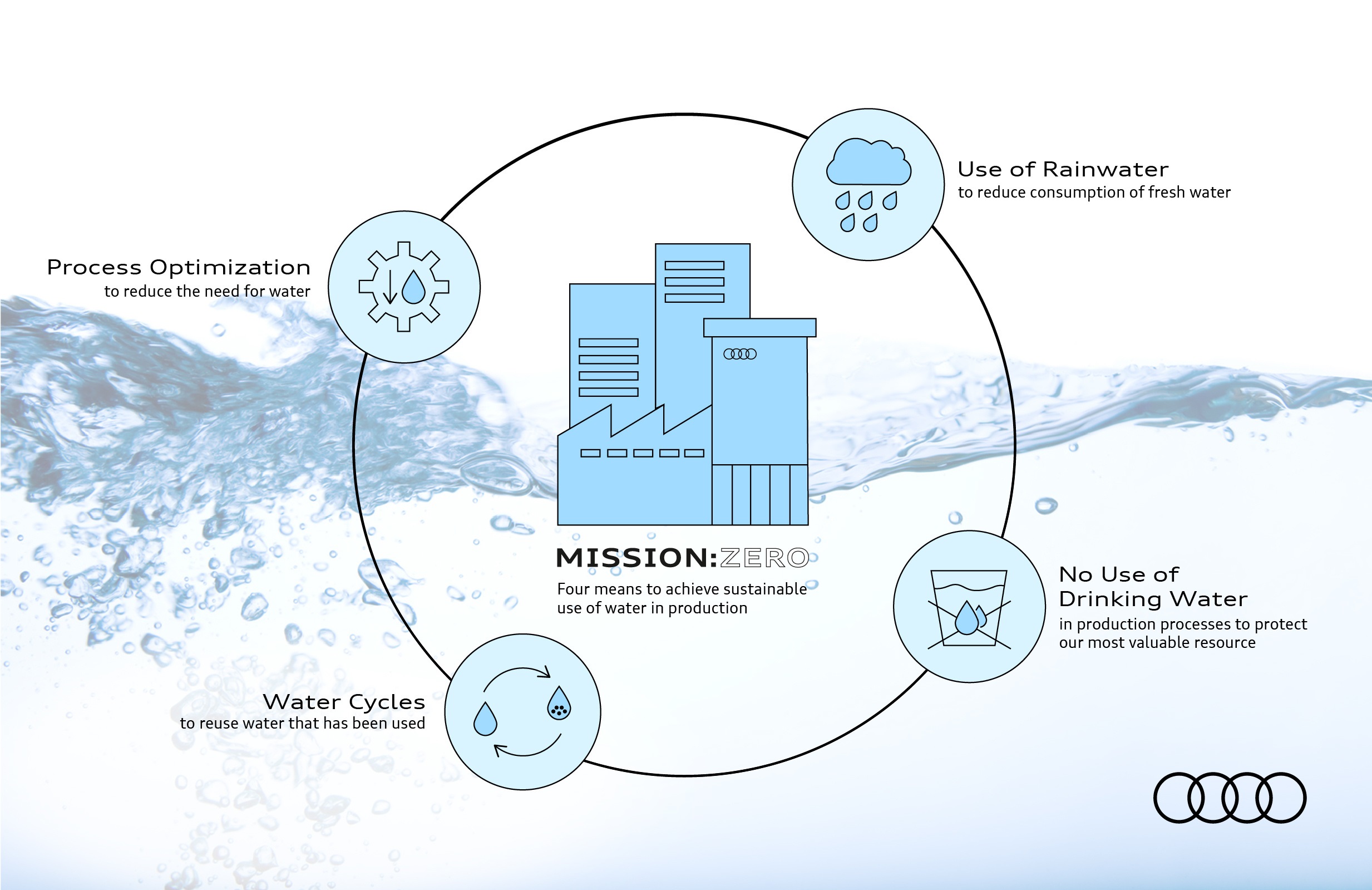