New battery farm will power production and grid at BMW Leipzig plant
30 October 2017
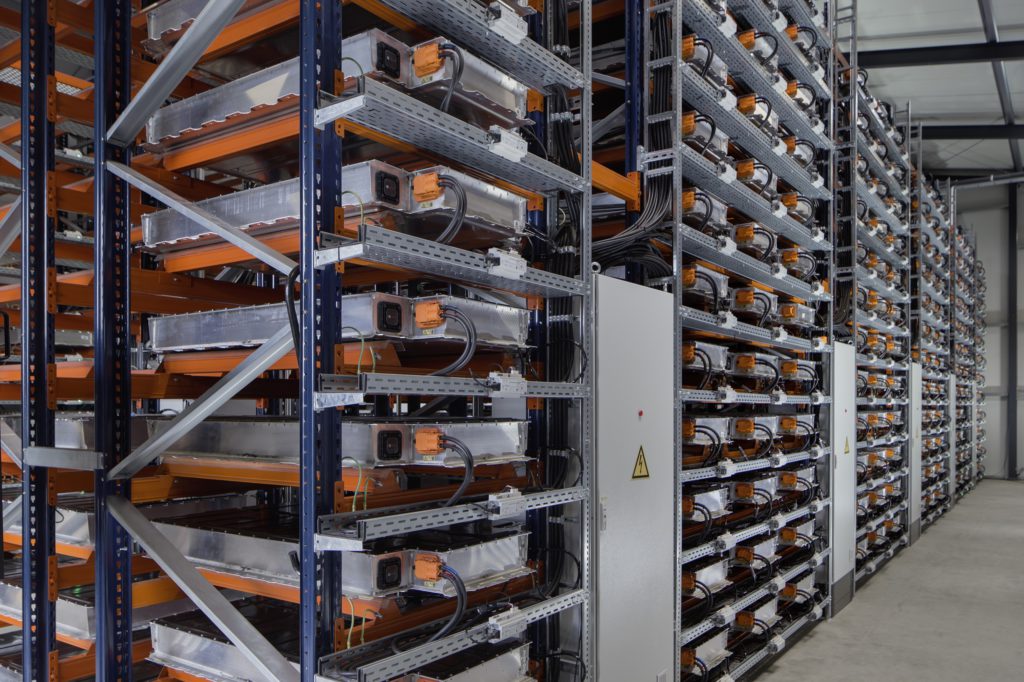
30 October 2017
BMW has commissioned a battery storage farm on the grounds of its plant in Leipzig, where second-life electric vehicle (EV) batteries can feed electricity grids through renewable energy.
As the automotive world increasingly goes electric, the question of what can be done with batteries once they have run their course in a vehicle is increasingly relevant. BMW’s farm can house up to 700 used batteries and will store electricity generated through wind turbines, powering electricity grids and production lines at Leipzig.
′The capacity of 700 high-voltage batteries is the equivalent of an electric range of 100,000km in a BMW i3. The scalable approach means that the storage unit could be further expanded to accommodate more batteries. It is also already compatible with upcoming battery generations and therefore future-proof,’ underlined Joachim Kolling, head of energy services at the BMW Group. ′We are demonstrating once again that the concept of sustainability at BMW i goes far beyond the car.’
The farm currently houses 500 new and used batteries, due to the fact that the electric i3 model has only been in production for four years, and many of them still have good life in their batteries. With wind turbines located on the grounds of the plant, the BMW Battery Storage Farm Leipzig links decentralised captive production from renewable energies with local energy storage and an industrial consumer in a completely unique way. The stationary battery storage farm is also integrated with the public power grid, which enables its electricity to be marketed as primary balancing power.
The German manufacturer is also celebrating the 100,000th i3 model rolling off the production line at Leipzig. At an event to mark the milestone, the BMW i8 Roadster, as a camouflaged prototype, was presented. Series production of this next model in the company’s i electric range will begin in 2018. This will kick-start the company’s second wave of electric powered vehicles, which BMW has invested in.
Meanwhile, as part of its effort to source cobalt from responsible sources related to environmental standards and human rights, BMW will increase the transparency of its own cobalt supply chain by the end of 2017, releasing information on smelters and countries of origin for raw materials.
The company is also currently working with an independent partner on a feasibility study to explore to what extent the social and ecological situation can be sustainably improved through model mines for artisanal mining in the Democratic Republic of Congo. The study is specifically evaluating whether local model projects could be implemented with the potential for scalability at a later date.
Ursula Mathar, head of sustainability and environmental protection at the BMW Group, comments: ′The BMW Group does not procure any cobalt itself; it only comes into contact with this raw material through the purchase of battery cells, for example. However, we are well aware that growing demand for electric vehicles also goes hand-in-hand with a responsibility for the extraction of relevant raw materials, such as cobalt. As a premium manufacturer – and in the interests of our customers – we aim to establish a transparent and sustainable supply chain that meets the highest standards.’
Photograph courtesy of BMW