Renault aims to achieve European carbon neutrality in 2040
27 April 2021
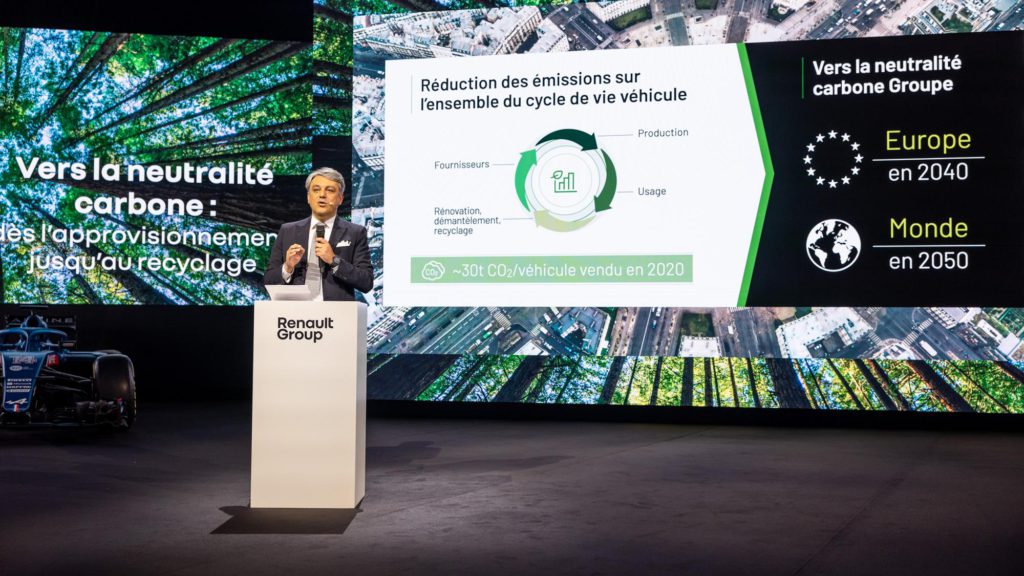
The Renault Group has announced its corporate social-responsibility (CSR) policy, which fits within the carmaker’s wider Renaulution strategy. The policy revolves around three core pillars; ecological transition, customer and employee safety, and inclusion. A key aim of the first pillar is for Renault to achieve carbon neutrality in Europe in 2040, and worldwide in 2050.
′We consider our environmental and societal responsibility as one of the chapters of Renaulution. Our commitments to reduce our carbon footprint, to the safety of people who use our vehicles and of employees in the workplace, and on inclusion meet our strategic challenges and support value creation. These commitments embody our purpose while contributing to the group’s transformation,’ said Luca de Meo, CEO of Renault Group.
65% electric vehicles in Europe in 2025
Underpinning the French carmaker’s ecological transition and efforts to achieve carbon neutrality, the core Renault brand aims for ′electric vehicles’ to account for 65% of sales in Europe by 2025, and 90% in 2030.
At first glance, Renault’s electrification plans are more ambitious than those recently announced by Stellantis, the company created by the merger of fellow French carmaker PSA Group and Fiat Chrysler Automobiles (FCA). Stellantis plans to generate 38% of its European passenger-car sales from electrically-chargeable vehicles (EVs) in 2025.
However, there is a key semantic difference as Renault includes standard, non-chargeable hybrids in its definition of electric vehicles, whereas Stellantis only counts battery-electric vehicles (BEVs) and plug-in hybrids (PHEVs), i.e. chargeable vehicles, in its target. Neither company has provided a detailed breakdown of the share targets for each powertrain type considered under their respective electrification targets.
The electrification targets of both companies are surpassed by Toyota, which plans to have a ′powertrain mix that is more than 70% hybrid by 2025; more than 10% plug-in hybrids and more than 10% zero-emission models.’
Further ecological-transition initiatives
In addition to vehicle electrification, Renault seeks to reduce its carbon footprint in the supply chain. The company will focus its efforts on six components, which currently account for 90% of the procurement carbon footprint – steel, aluminium, polymers, electronics, tires, and glass. By 2030, the carmaker aims to reduce the carbon footprint associated with components supply by 30%, measured as CO2 per kg of material.
The iconic Renault 5 is scheduled to return in 2025 as a BEV model, and will feature more sustainable batteries. These will reduce its carbon footprint by at least 20% compared to the brand’s current B-segment BEV offering, the Zoe. Renault is also working to secure a responsible and sustainable supply of minerals, exemplified by its partnership with Veolia and Solvay to recycle metals used in batteries, such as cobalt, nickel and lithium.
The French carmaker also aims to reduce emissions from its manufacturing facilities by 50% worldwide, compared to 2019 levels. It will invest €20 million in its plants to generate up to €90 million in savings, by reducing energy bills and avoiding penalties for excess emissions. The company’s three ′Electro-Northpole’ plants in the north of France (Douai, Maubeuge and Ruitz) will be carbon neutral by 2025, with other facilities in Europe following suit by 2030.
Customer and employee safety
The second pillar of Renault’s CSR policy centres around customer and employee safety. This entails reducing the number of road accidents and assisting emergency services, as well as striving for zero work-related accidents and illnesses.
Renault will analyse driving, road and traffic data to encourage safer driving, inform drivers of potential risks on their route, and to provide real-time warnings. A fail-safe mechanism on vehicles will trigger automatically in dangerous situations, with the ′Safe Guardian’ system slowing the vehicle down and returning it to a safe-driving mode.
From 2022, the Renault Megane-E will come equipped with an automatic speed-limit adjuster and its top speed will be capped at 180km/h. Future Renault and Dacia models will also not be able to exceed 180km/h.
To assist the emergency services, Renault has also developed two other innovations that will be fitted to future models. First, the ′Fire-fighter access’ system helps to put out accidental battery fires. It is already a feature on electric vehicles and will be added to all future electrified Renault models. Second, the ′Rescue Code’ is a QR code that helps first responders to identify a vehicle and access its structural information. In the event of a serious accident, it reduces the rescue time for a passenger by about 15 minutes.
Inclusion
The third pillar of Renault’s CSR strategy is inclusion, which focuses on employability, parity, and solidarity.
As vehicles become increasingly connected and electrified, the carmaker is creating a tertiary education centre. This will be dedicated to improving employee skills in electrification, data management, analysis and cybersecurity, and the circular economy, including engineering related to the recycling of vehicles and their batteries. The ReKnow University will train nearly 40% of the workforce affected by these changes by 2025.
Renault states that it has the largest proportion of female employees compared to other vehicle manufactures, but women still only account for 25% of its workforce. In order to achieve targets for gender balance, the company aims to promote women to ′key positions within the group, in governance bodies, the top 4,000, and the top 11,000. In each of these three categories, the group aims to have women making up 30% of its workforce by 2030, 35% by 2035, and 50% by 2050.’
The carmaker is also looking to uphold its position as industry leader when it comes to reducing the gender pay gap, ′which is already close to zero at group level and is set to hit zero around the world by 2025.’ By then, Renault ′will reach gender balance among apprentices and interns, thereby creating a recruitment pipeline and ensuring future generations are familiar with the trades of the industry.’