Reuse and recycle: a mantra for EV-battery manufacturing
18 March 2021
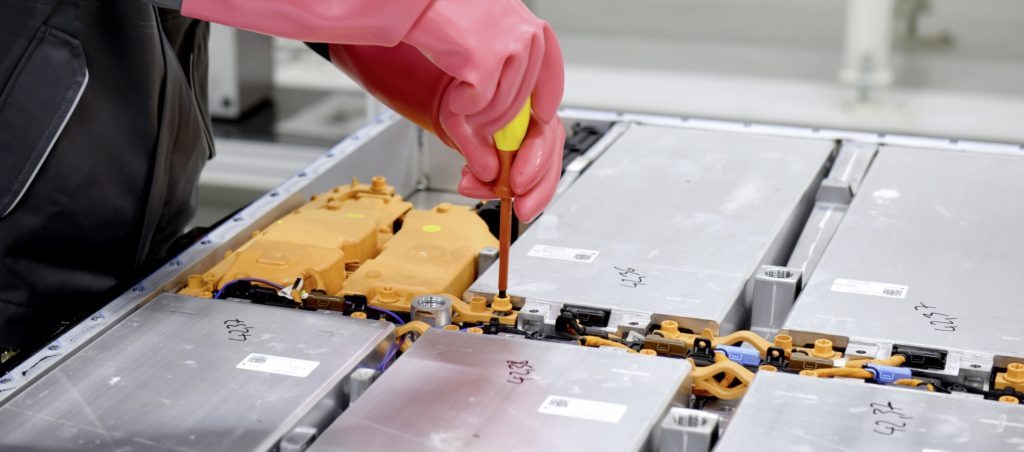
Electromobility is synonymous with sustainability. To ensure electrically-chargeable vehicles (EVs) address climate-change concerns across their lifespan, OEMs are charting roadmaps for battery reuse and recycling.
Renault recently joined forces with Veolia and Solvay to establish a circular economy for batteries. Earlier in the year, Volkswagen (VW) Group drew the curtain back on its recycling practices in Salzgitter. Meanwhile, Nissan has found a way to give used-Leaf batteries a new lease of life.
Recycling collaboration
Entering a consortium with resource-management company Veolia and the scientific solution provider Solvay, Renault’s latest partnership will stretch across the EV-battery value supply chain. The three companies will power up a circular economy through closed-loop recycling, aiming to preserve resources like cobalt, nickel and lithium, while also lowering emissions and creating value.
An existing consortium formed between Veolia and Solvay in September last year will be the basis of the new partnership with Renault. Metals that were previously recovered in a form only suitable for metallurgical applications can now be purified for reuse in new batteries, reducing the environmental footprint of EV batteries.
′We aim at implementing innovative and low-carbon battery-recycling solutions to pave the way to sustainable sourcing for strategic battery materials as electric mobility is growing,’ said Luca de Meo, Renault CEO. ′Together, we will leverage our strong presence on the entire EV value chain in Europe to take a competitive position in the battery-materials market and generate value beyond our core business.’
The three companies are already engaged in an experimental phase, which set up a pre-industrial demo plant in France to extract and purify end-of-life EV battery metals.
Breaking down the breakdown
VW began recycling batteries in-house at its Salzgitter plant at the end of January this year. However, only batteries that can no longer be used in any other way are sent for recycling. Therefore, the carmaker is checking battery modules to see if they can be given a second life in a mobile energy-storage system.
′Our goal is to create our own circular process in which more than 90% of each of our batteries is recycled,’ said Thomas Tiedje, head of technical planning at VW Component. ′We don’t want to hand the process over at any point but prefer to train our employees and thus make them fit for the future.’
Previously-used batteries have been recycled in what is known as a ′pyrometallurgical process,’ where they essentially end up in a blast furnace. Through this new approach, VW is recycling by separating out a battery’s components through dismantling, crushing and sieving.
The Group’s next steps will be to optimise the processes used in Salzgitter. As soon as the pilot plant has reached its capacity, larger plants will follow. Through this method, the manufacturer hopes electromobility can become suitable for mass production, despite limited raw materials.
Automated-guided vehicles
Meanwhile, Nissan has been taking used lithium-ion batteries from the Leaf to power automated-guided vehicles (AGVs), which help workers in factories by bringing them components. The carmaker currently uses some 4,000 AGVs globally, saving time on the factory floor and increasing efficiency.
The first-generation Leaf was equipped with a 24kWh battery. These lithium-ion packs were made by combining 48 modules. About eight years ago, Nissan’s engineers found a way to take three of these modules and repackage them to fit inside an AGV. Last year, they began using repurposed battery modules instead of new ones, to power AGVs, increasing sustainability.
The repurposed batteries also last longer. While lead-acid units were typically replaced every couple of years, repurposed ones are expected to last seven to eight years. Fewer batteries means less environmental impact for Nissan.
′Our customers benefit too. When used EV batteries become more valuable, trade-in prices rise’ said Masashi Matsumoto, who promotes AGVs at Nissan’s production technology research and development centre. ′With more ways to use batteries, the overall residual value of the Leaf has increased.’
According to Bloomberg’s Electric Vehicle Outlook, the number of EVs on the road globally will reach 116 million at the beginning of the next decade, from 8.5 million in 2020. If EVs want to hold on to their green credentials, reuse and recycle must become a life-cycle mantra, not merely an afterthought. Whether recycling is achieved through partnerships, in-house or via a wider repurposing, a roadmap will become increasingly important as OEMs recognise the value of components they might have otherwise thrown away.