Volkswagen strides forward with sustainability and efficiency goals
26 November 2019
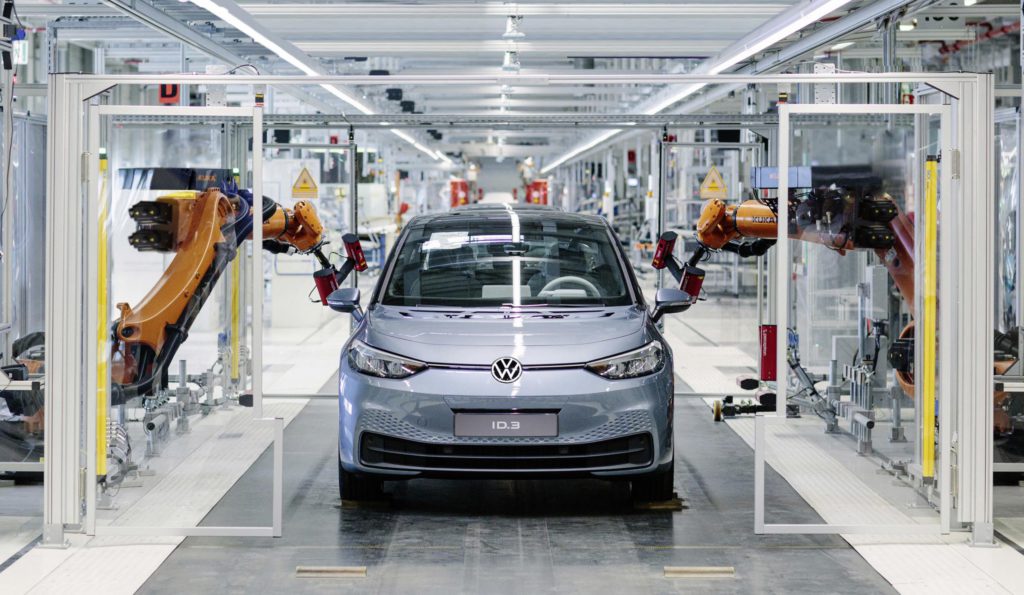
26 November 2019
Volkswagen (VW) is making fast progress towards its goals of creating a sustainable and efficient production environment, while also reducing overall production costs, it claims.
The carmaker recently stated its intention to become net CO2-neutral by 2050 as part of its ′goTOzero’ mission statement. It has set itself targets for reducing CO2 emissions of its fleet, which consists of almost 11 million new vehicles annually being manufactured in 122 plants worldwide.
VW’s first mass-produced electric vehicle, the ID.3, is built at the Group’s Zwickau plant with net CO2-neutral production.
′We are producing more environmentally friendly than ever,’ says Oliver Blume, member of the board of management of the Volkswagen Group and chairman of the board of Porsche AG. ′From 2010 to the end of 2019, the environmental impact per produced vehicle is expected to drop by more than 37%.’
Investment impact
To address offsetting trends, performance measures estimated at a cost of €1 billion are also being made in production, and productivity is increasing by 6%. At the same time, however, Blume emphasises that the carmaker must not neglect further efficiency measures.
′In pursuing the target of halving the environmental impact of production by 2025, Volkswagen Group is certainly in a better position now than planned, having attained a 37% reduction,’ he adds.
To achieve its goals, the VW Group is following five criteria in the assessment of environmental impact per vehicle: CO2 emissions, energy use, water use and solvent use, and generated waste. In the past two years alone, CO2 emissions per vehicle were reduced by more than 10%, the carmaker says.
The Group also states it is making good progress towards attaining the target of improving manufacturing productivity by 30% over the period 2016 to 2025.
This year, productivity is expected to be 6% above last year’s level, and production sites outside of Germany have made the most significant contributions. The improvement is better than originally planned.
Inter-group collaboration
Blume also highlighted how the Group could benefit from the versatility of its different marques. In a time when industry collaboration is at an all-time high, VW has the benefit of several different manufacturers under its umbrella, all with the ability to improve the company’s productivity.
′Inter-brand knowledge transfer and close cooperation are key factors of success in achieving further productivity increases and in reducing costs and investments,’ he states. ′It is becoming increasingly more important to replicate excellent examples and solutions and transfer them from one site to the others.
′We have 122 Group production sites worldwide. This production network offers tremendous potential for synergies. We continue to implement our production-strategy measures systematically.’