VW inks green steel deal for automotive manufacturing as it focuses on sustainable supply chains
23 March 2022
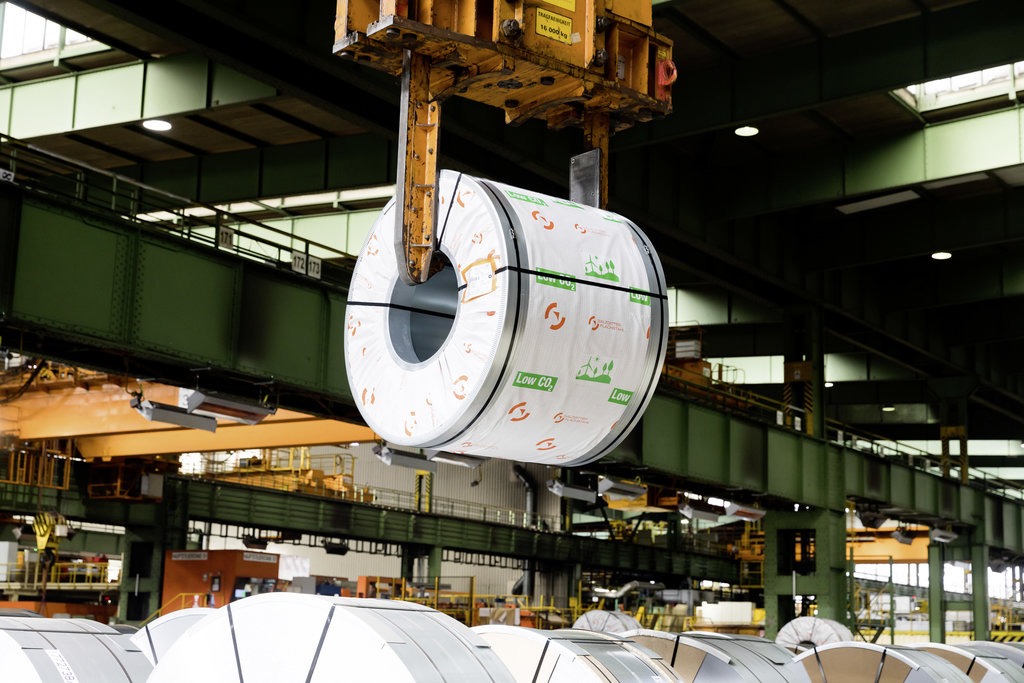
Volkswagen (VW) Group has inked a deal with German steelmaker Salzgitter to source low-carbon steel from 2025. The carmaker is increasingly shifting its focus to closed-loop recycling, wanting to slash greenhouse-gas emissions during the car manufacturing process. VW will use the steel for future automotive projects, including its new all-electric Trinity model that will go into vehicle production in Wolfsburg from 2026.
The two companies have signed a memorandum of understanding (MoU), with VW being one of Salzgitter’s first customers to benefit from the low-carbon steel that will be market-ready by the middle of the decade. BMW bagged a similar deal with the German supplier earlier this year in a bid to use more environmentally friendly steel at its European car-manufacturing plants.
Salzgitter is one of Europe’s largest steelmakers. The company has worked with VW for more than 60 years, with their latest MoU centring on decarbonising processes during vehicle production. Salzgitter believes that lower-carbon steel will allow for more than 95% of CO2 emissions in the metal’s production to be saved in the future, with the company betting on hydrogen and renewable energies.
‘Green’ steel
‘Purchasing is a decisive factor for the VW Group on the road to CO2 neutrality. And we want to achieve this goal by 2050 at the latest,’ said Murat Aksel, VW group board member for purchasing. ‘The further improvement of our CO2 balance, the use of materials, above all the raw material steel, plays a central role. The use of C02-reduced steel is an important step here, as is the recycling of steel residues.’
VW added that ‘greener’ steel, combined with closed-loop recycling, will help clean up supply chains, which remains one of the key challenges for carmakers on their way to carbon-neutrality. By the end of the year, both VW and Salzgitter will agree on purchase quantities for the low-carbon steel that will be deployed between 2025 to 2030.
Steel production, which is highly emission-intensive, has increased rapidly in the last decade, with Salzgitter planning to cut carbon emissions gradually by more than 95% by 2033. This would avoid 1% of Germany’s total CO2 emissions, it said.
‘The close proximity of steel and car production is another ecological plus of this planned cooperation,’ said Gunnar Groebler, chairman of the executive board at Salzgitter. ‘By supplying green steel and taking back the steel residues from car production, we are supporting our long-standing customer Volkswagen in achieving its climate targets. This is another very concrete step towards expanding and strengthening the market-based structures of the circular economy.’
Closing the loop
As part of the agreement, VW is also working on building a closed-loop recycling system for steel at its main plant in Wolfsburg. This will see the carmaker handing over steel residues to Salzgitter, which will melt these down before turning them into new steel products for car manufacturing. The goal is to expand circular economy strategies for steel to other VW sites in the future.
The German carmaker wants to put responsible sourcing at the centre of its supply chains. While steel plays a major part in car production, so do EV batteries. The company has set itself bold electrification targets, aiming to become the leader among EV sales in Europe. Hence, securing ethically-sourced battery materials is another important focal point for VW.
It recently joined a sustainable mining project, called the Initiative for Responsible Mining Assurance (IRMA), to help set standards in the sector and ensure raw materials in EVs are more sustainable. This comes at a time when big carmakers are increasingly feeling pressure from consumers and investors to meet stricter environmental standards.
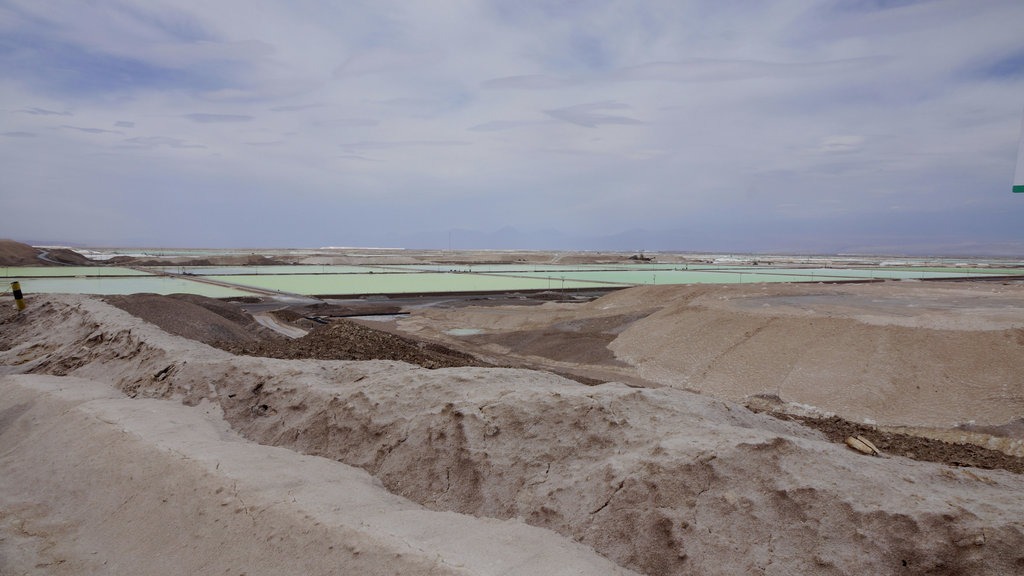
Source: VW
The initiative aims to improve industrial mining, which remains a ‘dirty’ business. With demand rising for battery raw materials such as cobalt, lithium, nickel, and graphite, greater corporate responsibility can help improve transparency along the automotive supply chains. This holds particularly true for conflict minerals, including tantalum and other raw materials such as aluminium, natural rubber, and leather.
‘The path to transparent and sustainable supply chains leads directly to the mine,’ said Aksel. ‘IRMA brings together all the important players: The raw material suppliers, the raw material buyers, workers’ representatives, civil society forces, investors and independent experts.’
VW says it is the first automotive company to publicly report on group-wide measures for the responsible sourcing of 16 raw materials.