Audi turns to trains for battery-module deliveries to lower carbon emissions
07 June 2022
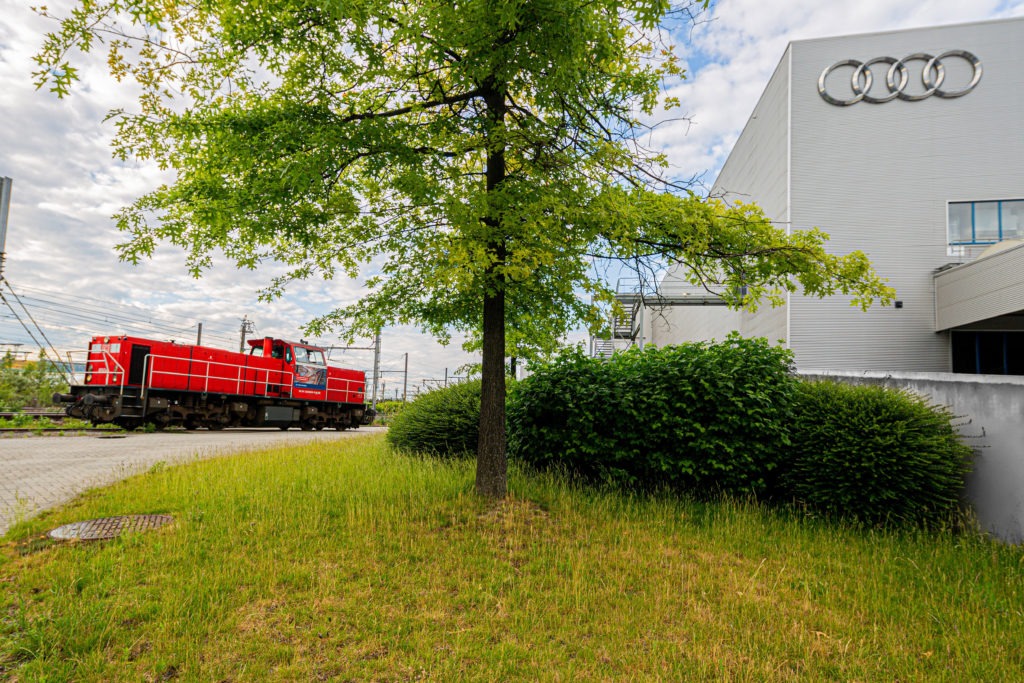
Audi will rely on rails to get its electric-vehicle (EV) battery modules from Hungary to Brussels. This move away from truck-based logistics is another push for sustainability. Turning to trains for this journey could save the Volkswagen (VW) Group brand up to 2,600 tonnes worth of carbon emissions a year.
While this looks to be an impressive number, it is the wider reach of this logistical decision that is more important. If the carmaker can successfully reduce its emissions by hitting the rails, this model could become the blueprint for how Audi ‘ships’ all its battery components. In helping to lower the carbon footprint of all its electric vehicles, the carmaker looks to make more ground on its cross-site environmental programme Mission:Zero.
From truck to train
Soon, battery components destined for Audi’s plant in Brussels will no longer arrive by truck from the company’s Hungarian-based supplier. Presently, up to 15 heavy-goods vehicles (HGVs) carry the modules and cells destined for the e-Tron and e-Tron Sportback over some 1,300km.
But looking to move these key electric-vehicle components via rail with DB Cargo, Audi expects to radically reduce its emissions as well as its outgoing costs. This switch from road to rail began in May 2022 and is due for completion by the beginning of next year.
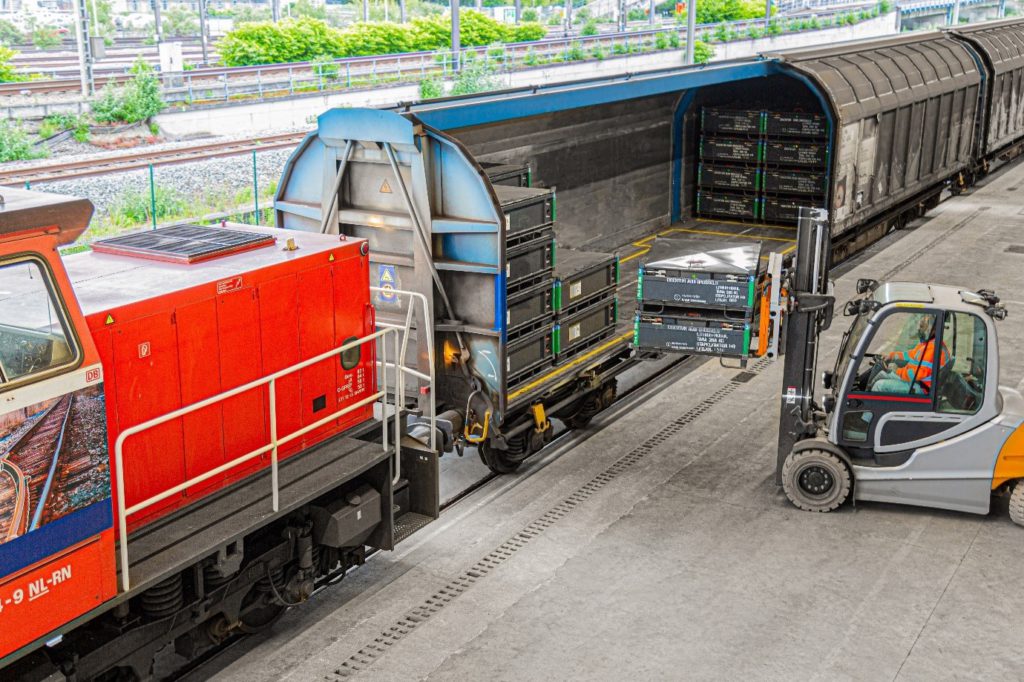
However, Audi’s battery supplier does not have its own rail siding. This has meant DB Cargo installing a weather-protected logistics centre at the Győr site in Hungary. This centre sees battery modules offloaded from trucks into rail cars ready for a 1,000km journey to Brussels.
Wherever possible, the carmaker uses DB Cargo’s ‘eco plus’ service. For example, sections of the route in Austria and Germany are powered exclusively by renewable energy including wind, solar and water. In Hungary and Belgium, Audi opts for DB Cargo’s ‘eco neutral’ package, with transportation power offset through climate certificates, reducing carbon emissions elsewhere.
The next stop
In the future, the carmaker would prefer all its production sites to implement rail-based solutions. In fact, by 2025, Audi wants all its high-turnover components like battery modules and cells to be delivered exclusively by train. ‘Brussels plays a pioneering role, but we developed this sustainable logistics concept for battery modules and cells in Audi’s entire production network,’ said Dieter Braun, Audi’s head of supply chain.
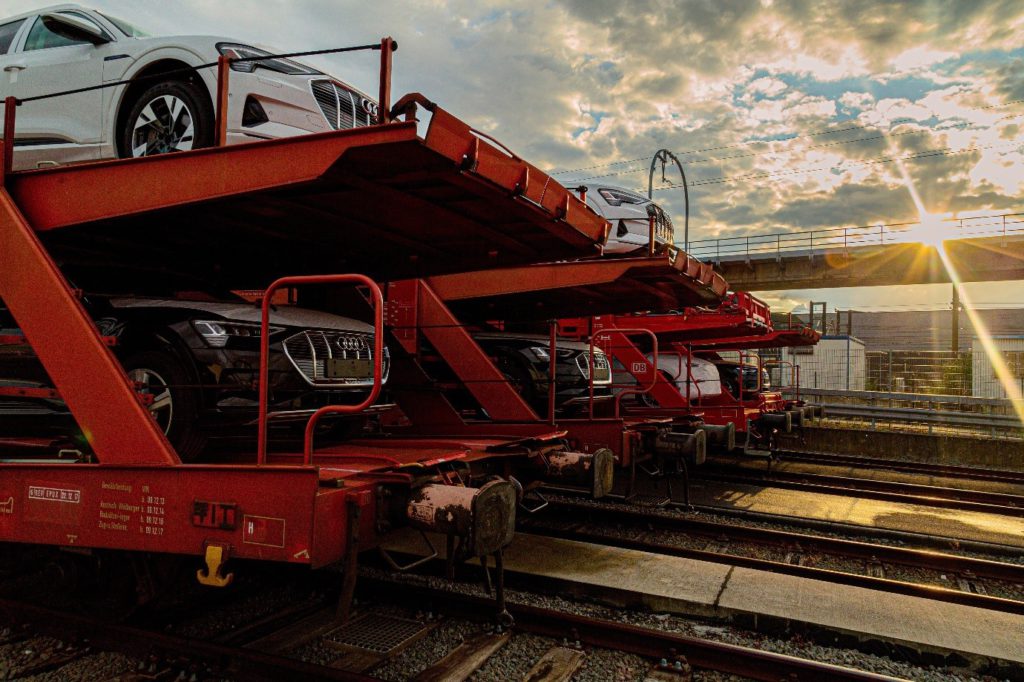
At the carmaker’s Ingolstadt headquarters, battery production is set up to start using modules and cells shipped by rail. These power units will then be used to build models on site with equipment and processes designed with this specific purpose in mind. Once these vehicles are built, they will likely return to the rails. Around 68% of Audi models in Europe already leave plants this way, a figure which is only expected to rise.
These plans dovetail with Audi’s environmental Mission:Zero programme, with the brand looking to go net-carbon neutral at all its sites from 2025. Audi considers net-carbon neutrality as lowering CO2 output as far as possible, then adjusting for the remaining emissions through compensation projects.
To achieve its sustainability goals, the carmaker has been investing heavily in cleaner technology and electrification. Audi is expected to spend €18 billion on electromobility over the next five years. This includes preparing plants for the switch, which the carmaker confirmed it is doing at its German Neckarsulm site with a new battery testing centre.
Aside from lower lifetime carbon emissions than an equivalent internal-combustion engine model, EVs also present an opportunity to support sustainability by reworking these manufacturing supply routes. Carmakers are going local for electric components, hoping to avoid complex and fragile supply chains. This means shorter journeys from plant to plant and lower logistical emissions.