Will 2023 see an end to automotive semiconductor supply shortages?
21 December 2022
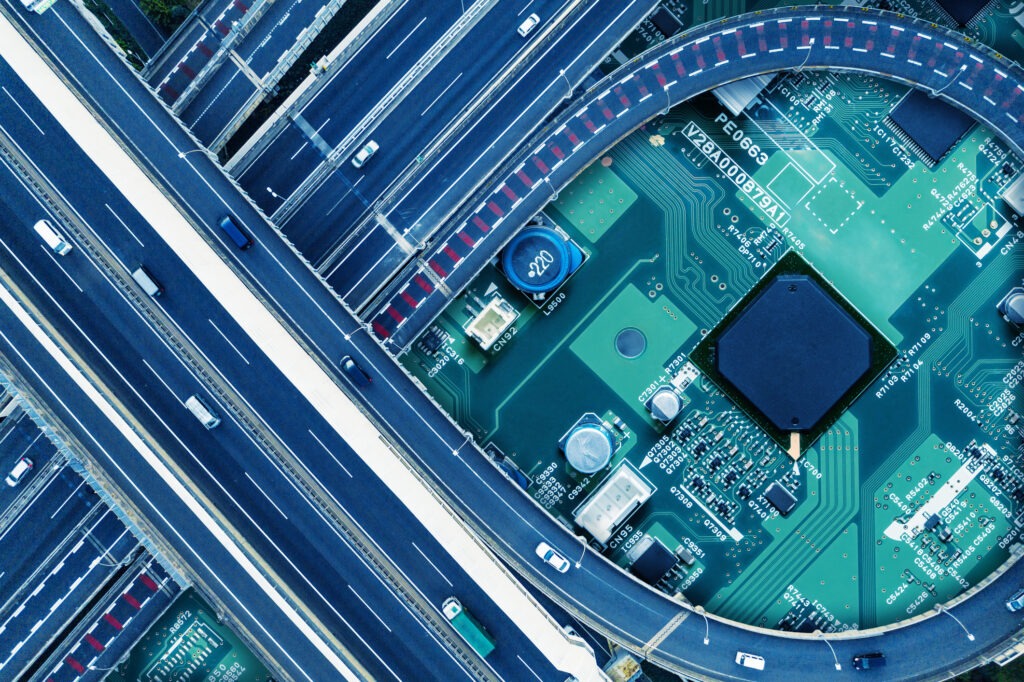
Semiconductor supply shortages continued to blight the automotive industry throughout 2022, but will 2023 provide relief? Autovista24 deputy editor Tom Geggus takes a look ahead.
To understand the current and future relationship between semiconductors and the automotive industry, a trip back to 2020 is necessary. Tom Blackie, CEO of VNC Automotive, unpacked the origins of the crisis for Autovista24.
The introduction of COVID-19 lockdowns in early 2020 brought with them a change in lifestyle as working from home became the new norm. This resulted in a spike in demand for electronic consumer goods, from office monitors to games consoles.
Meanwhile, other sectors like the automotive industry went into hibernation as plants paused production. ‘Traditional procurement practices kicked in and many contracts allowed OEMs to push inventory back down the supply chain and even cancel unwanted components for the period when no vehicles were being manufactured,’ Blackie explained.
So, semiconductor shipments to consumer-electronics companies far outstripped the automotive industry’s nearly dormant demand. Even the largest OEMs, moving some 10 million vehicles per year, appeared tiny compared to the billions of consumer electronics being ordered. This meant when carmakers returned to production lines, supplies were already bottlenecked elsewhere.
There has been a slow easing of this effect since then. However, as electrification accelerates and connected technology becomes more integrated, vehicle manufacturers will need an increasing amount of semiconductors.
A report published by Research and Markets estimates that the global automotive semiconductor market will grow from $41.8 billion (€39.2 billion) in 2021 to $47.71 billion in 2022 on the back of trends like these. While growth of this nature sounds promising, carmakers are still struggling to source the essential electronic components.
Wide-reaching crisis
Semiconductor shortages continued to plague the automotive industry throughout 2022. This meant short-term production adjustments impacted deliveries and created an additional hurdle for a besieged sector. When asked by Autovista24, a common theme to emerge from carmakers’ responses was the wide reach of the crisis.
‘This crisis concerns the whole automotive world, in the context of a pandemic that made the market fluctuate,’ a Stellantis spokesperson commented. Since the beginning of the COVID-19 pandemic, the 14-brand giant has been driving daily activity, plant by plant, by adapting to different market trends.
A Renault representative echoed this sentiment. ‘Like the entire automotive industry, we are affected by the semiconductor crisis,’ they said. ‘In order to manage this situation as well as possible, we have a daily crisis-management meeting to monitor and manage the evolution of the production situation, in particular with a week-by-week vision.’
BMW Group also made individual adjustments to its production programme throughout this year, acknowledging a corresponding impact on sales. ‘Although the company expects sales volumes in the second half of the year to be solidly higher than in the same period of the previous year, this will not fully compensate for lost volume in the first half of 2022. As a consequence, deliveries for the year are expected to be slightly below last year,’ a BMW spokesperson told Autovista24.
The manufacturer explained it can make adjustments at relatively short notice thanks to flexible production systems and work-time models. This will be vital as BMW expects semiconductors to remain in short supply in the coming months, with bottlenecks leading to additional production adjustments.
‘This year was full of challenges for the whole automotive industry, so semiconductors were only one part,’ a Volkswagen (VW) Group spokesperson commented. Both the war in Ukraine and COVID-19 have impacted global supply chains, with knock-on impacts for plants and strategic long-term planning. So, what does this mean for next year?
Expectations for 2023
Recent modelling by the Boston Consulting Group (BCG) found the global gap between semiconductor supply and demand currently sits at 9%, but this is predicted to decrease slightly next year. While capacities advance, however, not all industries will benefit in the same way.
‘The largest production capacity increases in 2023 are going to be for technology nodes below 16 nanometres (nm), which are not currently used in the automotive industry,’ Arturs Smilkstins, managing director and partner at BCG told Autovista24.
‘A 25% capacity increase is forecast for advanced (5nm to 7nm) nodes used in smartphones, whereas the 40nm node widely used in automotive microcontrollers (MCUs) as well as general purpose non-automotive MCUs, are only projected to increase by 4% in capacity next year,’ he added.
Accordingly, the semiconductor shortage is unlikely to disappear in 2023, Smilkstins said. While Europe has been slowly increasing its manufacturing capacity, it remains dependent on external supply and looks set to be so over the next few years. However, steps in the right direction are being taken.
The European Chips Act has raised hopes that the region will eventually become less dependent on external supply, although this will likely be felt some time after 2023. ‘The act’s provision for greater fab construction is likely to take four to five years to be completed, with new high-volume manufacturing (HVM) capacity from the constructed plants only becoming visible in 2027,’ Smilkstins said.
Stellantis’ spokesperson also acknowledged the likelihood for shortages to continue into the first half of 2023 at least. The carmaker does not expect the situation to be back to normal before the end of next year. Meanwhile, VW Group expects the situation to ease in 2023, both in terms of the number of critical semiconductor types and available quantities.
‘Nevertheless, we must continue to assume substantial bottlenecks in automotive-specific semiconductor technologies, as well as in high-voltage semiconductors used in both automotive and renewable energies. The right semiconductors in the right quantities will be the key for future development,’ the group’s representative told Autovista24.
But, VNC Automotive believes a more drastic shift could occur in 2023. The technology company foresees the cost-of-living crisis lowering demand for consumer electronics and inverting semiconductor shortages into oversupply next year and beyond.
New fabrication sites only look to increase this possibility, with many manufacturers investing heavily in new factories in recent years. However, these sites take several years to come online, meaning they might arrive at the bottom of the demand cycle.
‘Nonetheless, it is good to know there will be a future-proof manufacturing capability available to make the most advanced chips required for the emerging new applications, such as AI and the sensor fusion required for autonomous driving,’ said Blackie.
Figuring future frustrations
So, 2023 could mark the beginning of the end for semiconductor shortages, be that a slow return to stability or a total reversal of fortunes. But neither scenario comes without potential disruptions. Blackie highlighted geo-political tensions as a chief concern. Many countries are now keen on localised semiconductor production, to help prevent further supply-chain disruption.
‘While it is great that new state-of-the-art fabs are being built locally, it does not totally solve the issue as most products still use commodity chips that are mainly made in the Far East, of which the lack of supply can just as easily halt production,’ he said.
Smilkstins believes current investments will not bear fruit until the latter half of the decade. This includes the effects of the European Chips Act and its €45 billion investment. But even this might be lacking if Europe wants to build a more complete fabrication portfolio to bolster its independence.
Then there is the European energy crisis to consider, which could slow the progress of a more stable semiconductor supply, at least in the short term. ‘The energy cost in semiconductor manufacturing is already fairly high, at around 10%, and has risen to 20% this year,’ Smilkstins explained.
‘This cost will likely continue to rise as the energy crisis worsens into the winter of 2023. Much will depend on the actions of those in the energy industry and central government bodies when it comes to ensuring semiconductor manufacturing costs,’ he added.
Looking long term
When it comes to increasing the recovery rate, Smilkstins highlighted the need for forward planning. A clear understanding of future demand, potential problems, and design are of particular importance.
‘The automotive industry and suppliers of semiconductors must work together to move beyond the status quo and escape the semiconductor imbalances we see today. This collaboration must entail investment in, and planning for, the future to ensure the supply of semiconductors in Europe will once and for all overcome current vulnerabilities and be independent of outside influence and risk,’ he said.
Looking to secure semiconductor supply in the long term, BMW is adopting new approaches involving direct agreements with manufacturers such as Inova Semiconductors and GlobalFoundries.
VW Group has developed a cross-brand, cross-functional semiconductor strategy to guarantee long-term supply security. The carmaker also appreciates the need to understand the complexity of the component’s value chain, monitoring the market and production investments. The brand has effectively elevated its chosen semiconductor companies to the level of its tier-one partners.
‘Facing the transformation process and the continuously increasing demand for semiconductors in vehicles, the semiconductor topic will remain the central supply topic of the automotive industry in the coming years,’ the VW Group spokesperson said.