BASF partners in China to recycle rare-earth metals from car catalytic converters
15 February 2022
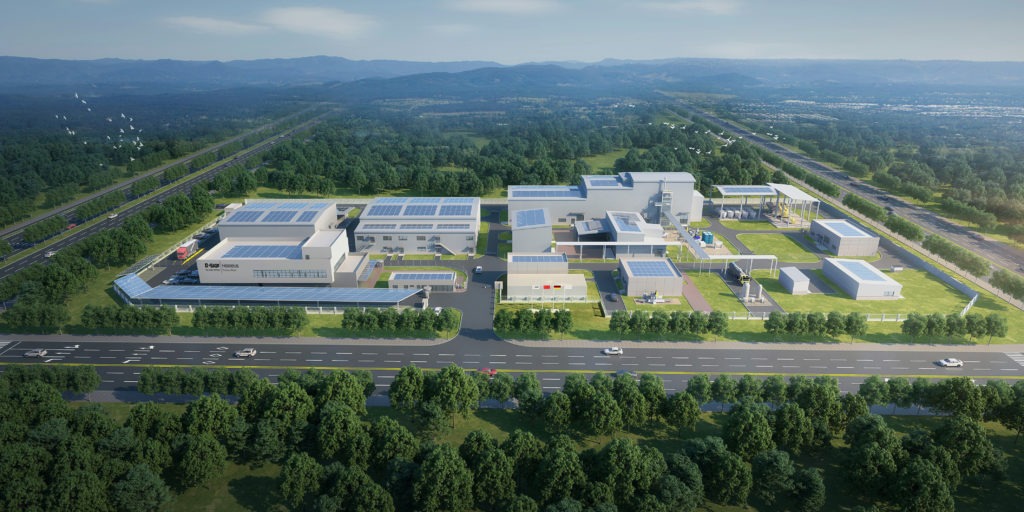
Disused battery cells from electrically-chargeable vehicles (EVs) are packed with valuable raw materials, making recycling a lucrative option. But more companies are looking beyond battery recycling to recover rare metals. German chemicals giant BASF has just formed a joint venture with tech group Heraeus to retrieve precious metals from spent automotive catalysts.
Rare-earth prices are surging, with demand continuously outstripping supply. Used in EV motors, these scarce metals are in high demand – not least because of buoyant EV sales in China. BASF and Heraeus now plan to set up a new company in the Chinese town Pinghu that will be dedicated to the recycling of rare-earths. Construction will begin this year, with operations kicking off in 2023.
Circular economy
Rare-earth metals are important to the move to green energy, with China often coming under the spotlight, as the country accounted for around 60% of global rare earths production in 2021. But the nation only has limited natural resources of platinum-group metals (PGMs), mainly made up of platinum, palladium, and rhodium.
The two German companies want to make use of pyrometallurgy, which treats minerals to bring about physical and chemical transformations that allows for the recovery of valuable metals. The focus will be on recycling scrap materials, including spent catalytic converters, to recover PGMs.
‘Through the partnership with Heraeus, we will bring best-in-class pyrometallurgy technology for the recovery of precious metals from spent automotive catalysts in China and help improve resource utilisation for high-tech and other companies that use precious metals,’ said Tim Ingle, vice-president, BASF precious metals refining, chemicals & battery recycling.
‘BASF’s leading position in automotive catalysts recycling and our combined expertise in precious metals will provide customers with a world-class circular economy solution to re-use precious metals in China.’
Securing stable supply
In order to secure supply of rare-earths, BASF last year said it would invest a double-digit million amount in capital improvements to increase refining capacity that would allow the company to recycle precious metals. The German firm is increasingly concentrating on precious metals recycling, including ones retrieved from industrial scrap. It recently acquired assets in Texas to expand its chemical catalyst recycling capacity.
BASF is also planning to build a battery-recycling prototype plant in Schwarzheide, Germany, to extract lithium, nickel, cobalt, and manganese from end-of-life lithium-ion batteries. Combined, these efforts help BASF meet the needs of its automotive OEM customers that are moving towards climate-neutrality in the coming years.
The automotive industry, including suppliers, is increasingly shifting its attention to more sustainable business practices – and circular economy strategies are key to decarbonise the mobility sector. BASF and Heraeus said the precious metals they plan to recover would be used to make new products for the automotive, chemical, electronics, and green hydrogen industries. The CO2 footprint of these recycled metals is more environmentally friendly by as much as 90% compared to primary metals sourced from mines, the companies said.
‘This joint venture builds on our already strong presence in China within the wet-chemical recycling industry,’ said Marius Vigener, vice-president business line chemicals at Heraeus Precious Metals. ‘Recycled precious metals minimise emissions and will enable our customers to reduce their CO2 footprint. This will support China in the development of its circular economy and contribute significantly to the stability of local precious metal supplies.’