BMW’s new competence centre to give cell suppliers an EV-battery blueprint
25 May 2022
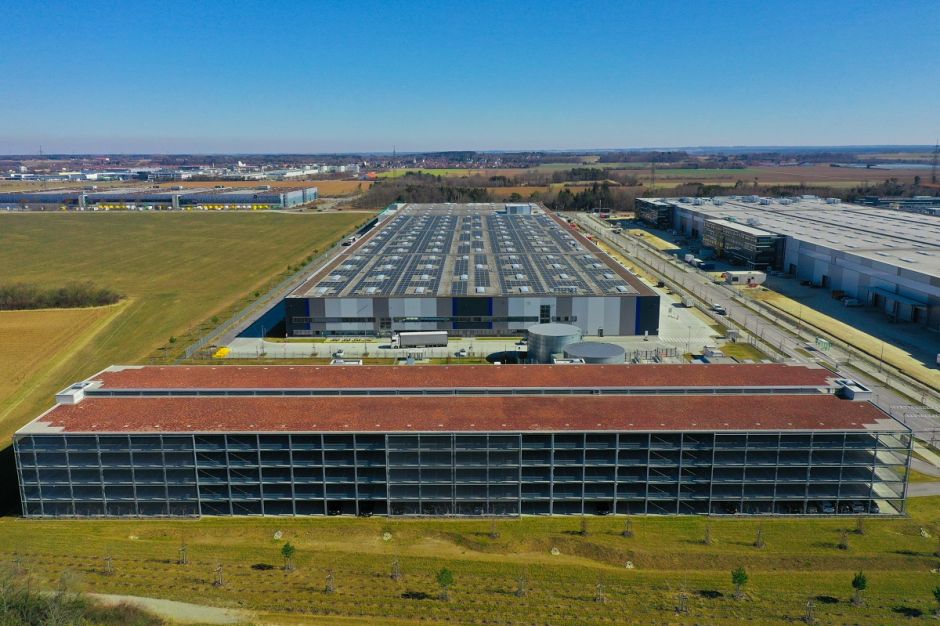
BMW Group is to open its Cell Manufacturing Competence Centre (CMCC) this autumn, as it continues to develop in-house electric-vehicle (EV) battery understanding.
The facility in Parsdorf, Munich, will allow the German carmaker to demonstrate the industrial feasibility of future generations of high-performance battery cells. The pilot line at the competence centre will make it possible to analyse and fully understand cell value-creation processes. This will enable future suppliers to produce cells to BMW Group’s own specifications and thereby optimise battery-cell production with regard to quality, output, and costs.
The competence centre is BMW’s answer to EV-battery development. Unlike some of its domestic rivals, the carmaker has ruled out establishing its own gigafactory for large-scale EV-battery manufacturing. Instead, it aims to give suppliers a blueprint of what it requires when it comes to energy storage for its growing electrified vehicle range.
Staggered approach to initial production
Investment in the initial development phase for the CMCC totalled around €170 million. About 80 employees will work at the Parsdorf facility, which is supported by the German Federal Ministry of Economic Affairs and the Bavarian Ministry of Economic Affairs, Regional Development and Energy, within the framework of the Important Projects of Common European Interest (IPCEI) funding process.
Due to the complex technologies involved, battery-cell production will be commissioned in stages, with production due to start at the CMCC in the autumn. In the initial phase of the ramp-up, the systems for electrode production will be installed and run in. During this stage, raw materials, such as graphite and nickel oxides for battery electrodes, are metered and mixed. This is followed by metal foil coating and final compression.
In the second phase of production at the plant, the systems for subsequent cell assembly and formation will be installed. In this step, the electrodes are processed with other sub-components to create battery cells and are formed and checked for quality.
The entire build-up of cell manufacturing at the facility will take about a year. Following this, near-standard battery-cell production at the competence centre will transition to regular operation, a process BMW believes will take another 12 months.
Production for the future
The site will also focus on innovative processes and systems that can be used in standard production. The BMW Group will produce battery-cell samples at this site for the next generation of battery technology for use in the carmaker’s Neue Klasse (New Class) of vehicles. The aim is to significantly increase the energy density of the next generation of lithium-ion cells and, at the same time, reduce materials and production costs.
As is key in all BMW’s future production plans, the facility will rely on renewable energy, including photovoltaic systems on the roof of the building.
‘The CMCC will enable us to round out our know-how throughout the value chain, from battery-cell development to production of modules and powertrain components, up to and including installation of fully-assembled high-voltage batteries at our vehicle plants,’ stated Markus Fallböhmer, head of production engines, e-drives at BMW Group. ‘Standard production in Parsdorf will create an authority in battery-cell production. This means BMW Group experts will be able to discuss topics with cell manufacturers at the same eye-level and optimise processes and technologies.’
A different view of gigafactories
While other carmakers are building their own gigafactories, taking control of the supply chain for this crucial element of electric vehicles, BMW is choosing to continue working with external partners. The company has signed a contract with Swedish startup Northvolt, with deliveries starting in 2024. The value of this contract is around €2 billion and will see batteries manufactured with renewable energy.
This strategy keeps expenses down. It costs a large amount to build a gigafactory, source equipment and staff, and buy materials for cell production. However, this strategy is not without risks, as quality control of cells is out of the carmaker’s hands. The establishment of the competence centre mitigates this risk, allowing BMW to develop the technology and hand it over to selected partners for mass production.