Fuel cell toolkit to help reduce production costs
14 June 2021
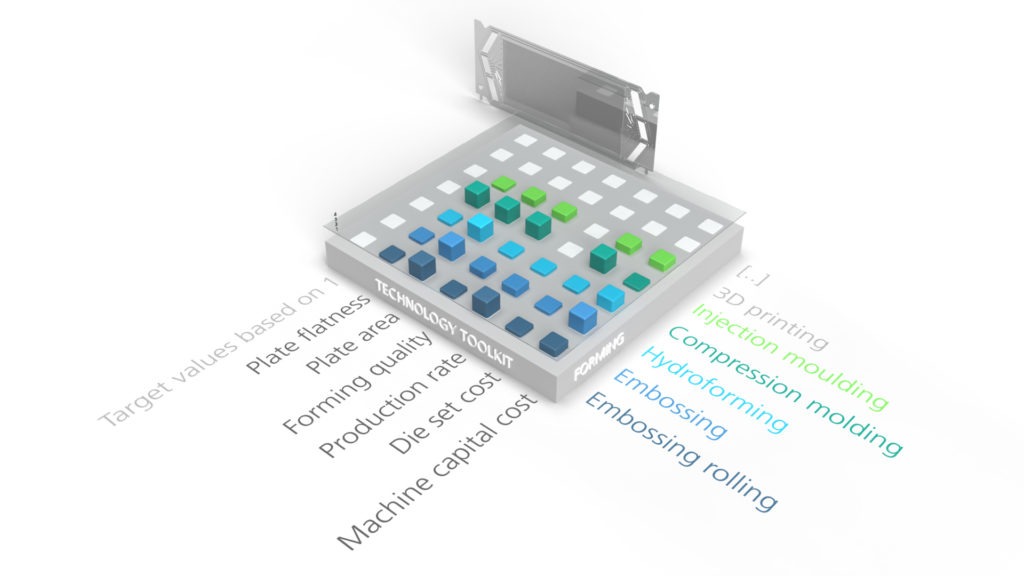
As the interest and need for hydrogen fuel cells grow, the need for cost-effective mass production must be addressed. Therefore, the Fraunhofer Institute for Machine Tools and Forming Technology (IWU) and the Fraunhofer Institute for Production Technology (IPT) will distil their expertise in the field into a shared virtual-technology toolkit.
According to the institutes, there is a need for cost-reduction in the production of the bipolar plates within fuel cells. These are a central element of fuel cells and control the supply of hydrogen and air, as well as the extraction of steam and energy.
The design of the flow fields that reflect channel structures in the plates is particularly important, as the gases involved in the conversion process, to produce electricity, flow come through these. The larger the surface area and the flatter the plates, the better they can interact with other components, increasing efficiency. It is in the area of flow plates that the IWU and IPT have expertise.
‘The companies that reach out to us are usually looking to invest in the production of fuel cells. They have some basic ideas about what the forming process will involve but are not sure what the economic consequences of using this process will be. For example, production rates and manufacturing costs are particularly difficult to assess,’ explained Ulrike Beyer, head of the TaskForce Hydrogen@IWU.
‘Using our technology toolkit, we can apply evidence-based analyses to observe the initial situation, taking in all the possible outcomes, and consider the various dependencies systematically. This allows us to develop a tailor-made technological solution for any needs,’ he added.
Vehicle-cell design
Alongside investment in machining, die sets, and the production quantity, the researchers must also factor in the forming results that can be achieved, such as size, flatness, and flow field design.
The raw material used also influences the choice of forming process, and can increase costs. ‘Originally, we mainly worked with composite materials,’ explained Christoph Baum, managing director of Fraunhofer IPT. ‘These ensure that the fuel cells have a long service life, but they only have limited suitability for mass production because they require more effort and are more expensive to produce. In addition, with composite materials, the material thickness remains rather high, even after processing. This means any fuel-cell stack quickly becomes very large, which makes them impractical for use in vehicles. This has led to us increasingly using materials like steel, usually achieving better and more cost-effective results.’
With OEMs looking at the development of hydrogen fuel cells as an another potenial drivetrain alongside battery-electric vehicles (BEVs), the toolkit could reduce the components’ cost while increasing the quality. By making the cells lighter and smaller, they can also help reduce vehicle weight and therefore increase range.
Not only will this have a benefit on performance, but it could also have an environmental impact. This is because lighter zero-emission vehicles will be easier on tyres, for example, reducing particulate expulsion from the rubber as it wears.
There are plans to expand the technology toolkit in the medium term to include additional production steps and fuel-cell components in cooperation with other Fraunhofer Institutes. ‘Our goal is to create a large overarching digital platform that allows individual production steps to be viewed and combined with each other in order to find the optimal combination for producing a complete fuel-cell for a specific situation,’ said Beyer