What is a gigafactory?
16 July 2024
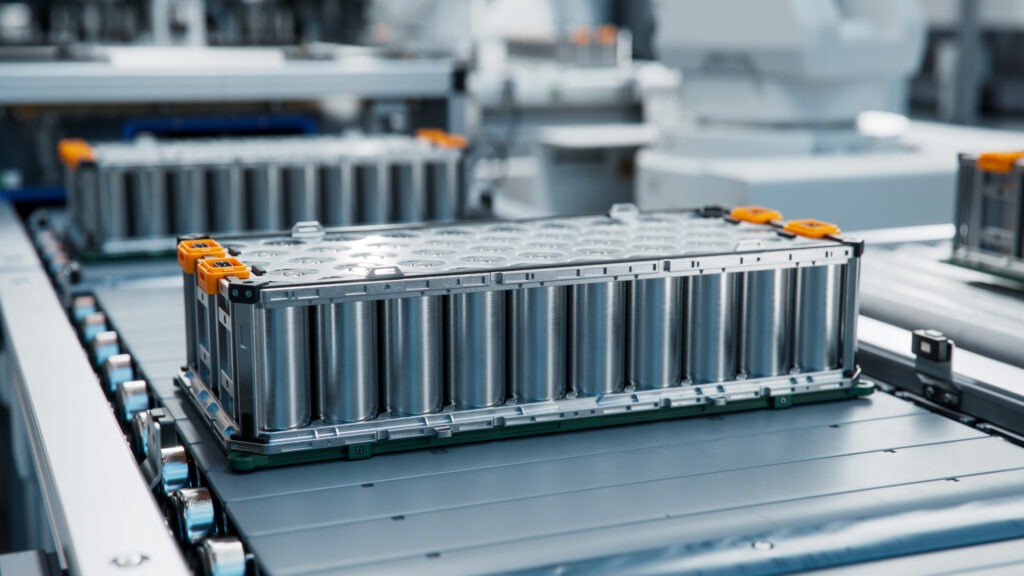
What is a gigafactory, and why are they so important to the future of the battery-electric vehicle (BEV) market? Autovista24 special content editor Phil Curry explains the terminology, and what they do.
With the volume of BEVs increasing in Europe, there is a growing need to establish a localised gigafactory network. This will help to stabilise supply chains, which currently depend on imports from Asia.
Gigafactory importance
Gigafactory is the name used for an electric vehicle (EV) battery manufacturing plant. These sites do not produce vehicles, but instead supply the battery technology which powers hybrids, plug-in hybrids (PHEVs) and BEVs.
The term ‘gigafactory’ is often credited to Tesla CEO Elon Musk. It comes from a combination of the word ‘giga’, meaning a measurement multiplied by a billion, and the general term ‘factory’.
With EV numbers increasing globally, more gigafactories are needed to ensure manufacturers can provide the required battery capacity. Governments, carmakers and batter suppliers are looking for suitable locations for new gigafactories, which will feed into local supply chains and benefit economies.
In 2023, the EU Commission approved €837 million of state aid to support the local production of EV batteries in Spain. Volkswagen (VW) Group is building a gigafactory in Valencia, and Envision AESC announced the construction of gigafactories in Cáceres. In the UK, Nissan is building a gigafactory next to its Sunderland vehicle plant. Meanwhile, in Germany, Tesla has already established a location just outside Berlin.
With companies like Northvolt, CATL, and SK On developing plans for local gigafactories, the European battery-manufacturing network is growing. This is especially important for adhering to Rules of Origin legislation, which is due to come into force in 2027.
Leading by capacity
The output of a gigafactory is not measured by the number of units produced. Instead, the total power capacity of the units it can manufacture measures output.
At any one time, a gigafactory may be manufacturing smaller-capacity cells for hybrids or larger-capacity units for BEVs. Therefore, the overall capacity of the factory is given to highlight its production potential. This is measured in gigawatt hours (GWh). If a factory is producing batteries with an average capacity of 58kWh, then a 1GWh gigafactory could provide cells for around 17,000 BEVs.
This measurement of capacity is also used to quantify the volume of cells produced by suppliers. Therefore, calculating which manufacturer made the most EV batteries is a question of power capacity, not the number of units.
According to data from EV Volumes, Chinese company CATL produced the most cells in terms of power capacity in 2023. The manufacturer utilised its gigafactories to produce 243.3GWh in the year, taking a 36% share of the market.
BYD was some way behind in second place. It produced a cell volume worth 117GWh in 2023, securing a 17% share of the market. In third, with a volume of 106.8GWh, was LG Energy Solution. In total, the manufacturer claimed 16% of the EV-battery market last year.
The figures show that the EV market is currently very reliant on battery production in Asia. While efforts are being made to expand the supply chain globally, it may take several years before a level playing field is established.
Complex construction
The complex nature of battery manufacturing means that a gigafactory is not simply a production line, running from beginning to end.
Inside the factory are several facilities. These include multiple manufacturing lines, clean rooms free of particulates, temperature and humidity-controlled dry rooms, assembly plants and testing laboratories. The make-up of a gigafactory is similar to production locations for semiconductors.
This means that building and developing a gigafactory is tricky. Speaking at MOVE 2023 in London, Lars Carlstrom, CEO of Italvolt and Statevolt explained how long it can take. 18 months is needed to build a gigafactory from scratch, followed by 15 months to reach full production capacity.
With the time taken to secure various permits and permissions, it could be three years before a gigafactory is ready to meet its supply requirements.
A gigafactory also needs to be future-proof. Funds can be wasted if a site cannot build relevant battery technologies because it has not kept pace with developments. One example is solid-state batteries, which several manufacturers are developing.
Offering shorter charging times and increased vehicle range, this technology is likely to be important to the future of the BEV market. Should a gigafactory not future proof its production lines for this new technology, it could be left producing out-of-date batteries that no vehicle manufacturer wants to use.