What is the automotive supply chain?
07 July 2022

The automotive industry is going through a supply crisis, with a shortage of semiconductors and the Ukraine war disrupting shipments of key components. These issues highlight the frailty of the automotive supply chain, but what is this, and why does a disturbance in one area cause severe delays across the entire sector? Autovista24 Editor Phil Curry untangles the web of confusion around supply chains in this latest explainer video.
Vehicle manufacturers run their plants based on the ‘just in time’ delivery of parts. A car can be made from up to 25,000 separate parts, and many of these are built from various components. A braking system, for example, features callipers, pads, pistons, link pins, discs, brackets, and more.
Each component needs to be sourced and manufactured, but they too rely on other suppliers, fabricators, and raw materials suppliers. The movement from each stage along the path from material to vehicle installation, and then onto the customer, is known as the supply chain.
Many years ago, this was an accurate term, with one company feeding into another, and another. However, today the automotive industry makes use of multiple suppliers, with the possibility of drawing from numerous companies. This leaves today’s chain looking more like a web, with so many interlinked stages all going into the same end product.
Semiconductors highlight supply-chain frailty
Like a chain, however, links can be fragile. Should one break, it compromises the integrity of the rest of the chain. This is a major reason for current delays in vehicle production, with some customers having to wait up to a year for delivery. The semiconductor crisis, which began in 2021, is a good example of the frailty of the automotive supply chain.
During the height of the COVID-19 pandemic, consumers increased their spending on electronic gadgets. This meant more semiconductors were redirected to consumer goods, putting pressure on all manufacturers of the critical components. The automotive industry is a virtual newcomer to the semiconductor market, and suppliers had to prioritise who they shipped the components to.
Semiconductors are not easy to produce, requiring a detailed level of fabrication that does not lend itself to high-quantity increases upon demand. Therefore, semiconductor-dependant automotive components cannot be built while they wait on supplies, and the related parts are destined for delay. This means the vehicle needing these parts will also go unbuilt. One break in the supply chain has consequences further down the line.
Tiers of suppliers
Suppliers can be categorised into three tiers, depending on what they offer to the market, and their relationships with the automotive industry.
Tier three suppliers deal with raw materials, such as minerals, metals, and plastics. Tier two suppliers make needed parts, but their components are not limited to just cars, they also supply to other industries. Semiconductors suppliers would be classed in this bracket, supplying to electronics companies and others who require the technology.
Finally, tier one suppliers build and supply finished components to carmakers ready for vehicle assembly, and often have direct relationships with manufacturers. Examples of this would include battery gigafactories, panel suppliers, and automotive systems developers.
Improving supply-chain reliability
The automotive supply chain is an integral part of the industry and one which carmakers cannot have full control over. Digitalisation is helping to improve tracking of materials and components, yet even if manufacturers owned every company that supplied their factories, external factors can also play a disruptive part. One example is the blocking of the Suez Canal in 2021, which caused supplies to be delayed as ships diverted.
However, carmakers can work with local suppliers to shorten supply lines, which not only improves reliability, but also reduces the carbon footprint of the process, a critical point in today’s eco-conscious world.
Autovista24’s What is? series explains some of the most important automotive terms and technologies used in the industry. Features on demand, semiconductors, over-the-air updates (OTA), bi-directional charging, electric vehicles (EVs), type approval, autonomous technology, seasonally-adjusted annualised rate (SAAR), total cost of ownership (TCO), and residual values (RVs), have all featured so far.
Make sure to subscribe to the Autovista24 YouTube channel and sign up for notifications. If you enjoy a video, give it a like and a share. You can let the Autovista24 team know what other automotive terms you would like defined in a future What is? video, or even recommend a subject for the next in-depth podcast discussion. All you need to do is head over to our Twitter, LinkedIn, or YouTube profiles and leave us a comment.
Transcript – What is the automotive supply chain?
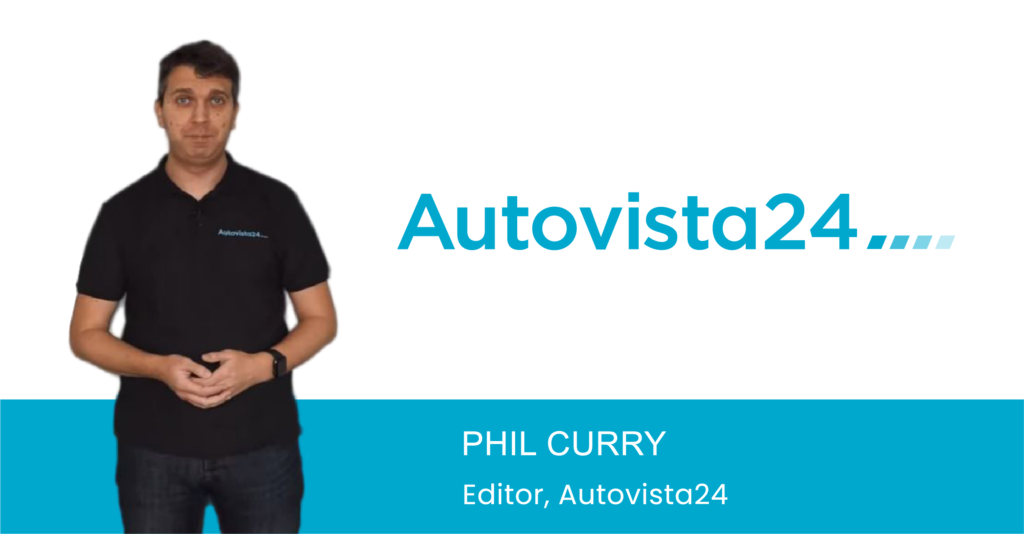
What is the automotive supply chain? I’m Phil Curry here with another of Autovista24’s explainer videos. Cars are built from parts. Parts are made from components and components are formed from materials. Suddenly the thousands of parts in a single vehicle and that can be anywhere between fifteen thousand and twenty-five thousand, can have many many steps for procurement, shipping and manufacture.
Bringing these components from one step to another is known as the supply chain. While in the past it may have been accurate statement with one supplier feeding into another and another and so on, today’s markets are dependent upon multiple suppliers each feeding into different stages of manufacture making it more of a supply web than a supply chain. However, like a chain there are multitudes of links and should one of these links fail it can make the entire chain fragile causing it to break. The automotive supply chain is therefore crucial for car makers ensuring they get the right parts at the right time to deliver their cars to the customers.
Let’s look at a basic example. Raw materials are shipped to a refinery which then ships them to a component supplier. This company receives other materials and builds its components. The part is then shipped to an engine supplier who puts it in a new unit and then ships it to the car factory where there it is put into the vehicle and sent to the dealership to be given to the customer. Between each of these steps however there were logistics and storage to take into account. It’s also worth noting that suppliers may have multiple companies feeding into them making the automotive supply chain very complex.
Now, there are different tiers of suppliers depending on their position in the supply chain and their status. Tier 3 suppliers are those who deal with raw materials such as minerals, metals and plastics. Tier 2 suppliers make needed parts and components but they are not limited to just cars, they can also supply to other industries. Electronics and semiconductors are an example of this. Tier 1 suppliers are those that build and supply finished components to car makers ready for vehicle assembly and often they have direct relationships with vehicle manufacturers themselves.
While car makers try to control as much as possible within the automotive supply chain, they are very reliant on external companies for certain aspects of it. This means the slightest disruption being shipping, manufacturing or sourcing materials can affect the rest of the chain. One example is the blockage of the Suez Canal in 2021 which held up components making their way to car factories in Europe. Another is the current semiconductor crisis. Whilst the materials of semiconductors are there, tier 2 suppliers are unable to meet demand from all markets and automotive is one of those suffering. This is an example of a weak link. Raw materials may be available but the components that need semiconductors cannot be made, meaning everything further down the supply chain is delayed as well. The longer a supply chain in the number of numbers and distance, the more difficult it is to control and manage. In a world where car makers are striving to reduce CO2 emissions, shortening the supply chain by manufacturing components in-house and working with raw materials suppliers closer to home pays dividends when it comes to a quick reliable and clean image.
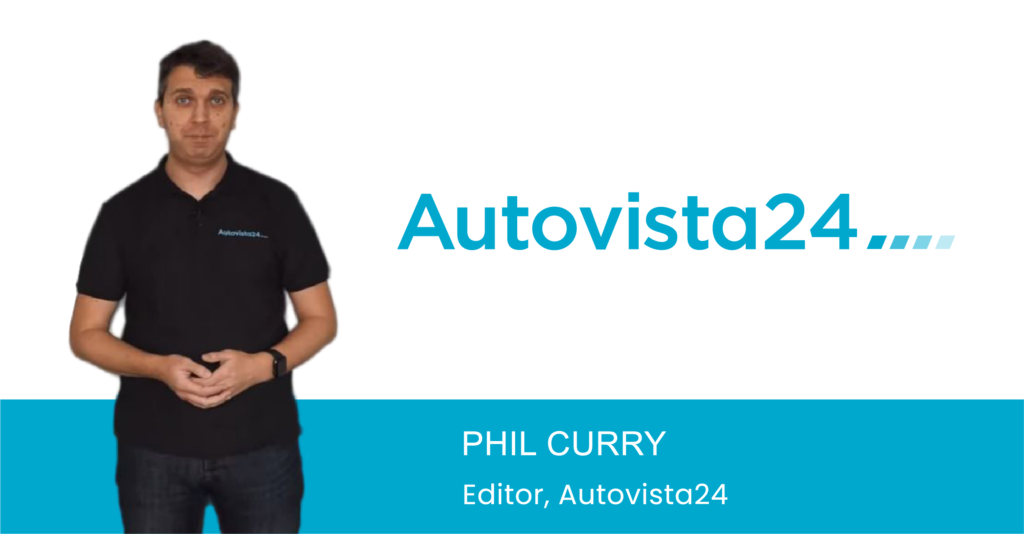
The automotive industry is a very challenging one and there are many terms that Autovista24 is looking to explain in this series. If you can think of anything you want to be discussed please drop us a line in the comments below or in the contact details available at autovista24.com. While you’re there don’t forget to sign up to our daily email and check out our Twitter and Linkedin pages. Thanks for watching.