Carmakers producing PPE in fight against coronavirus
15 April 2020
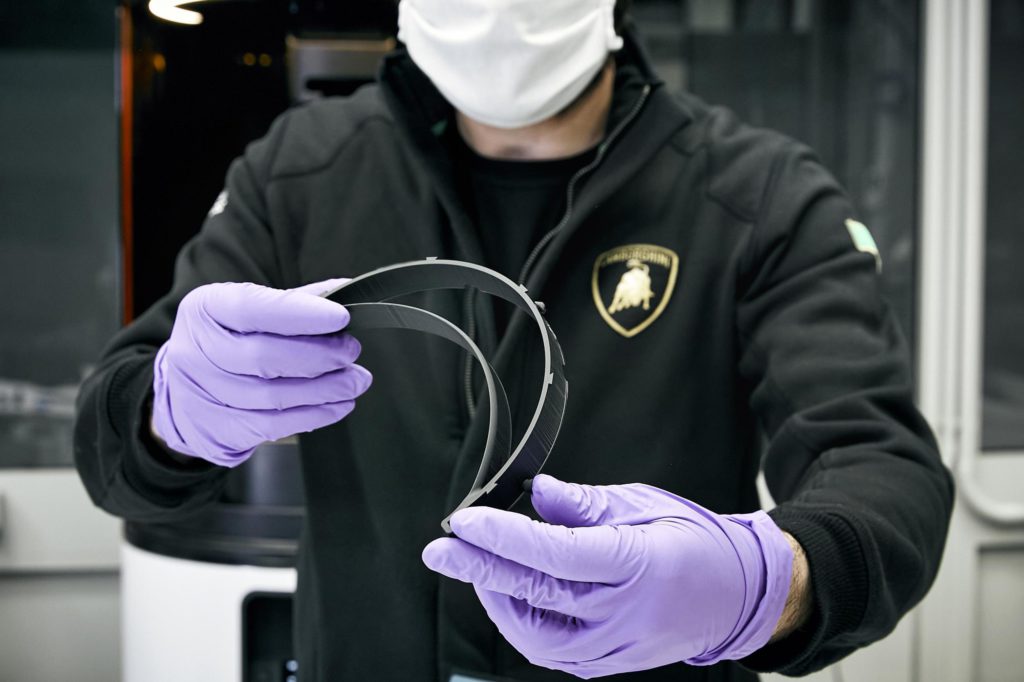
15 April 2020
In the early days of the coronavirus (COVID-19) pandemic, much was made of the need for ventilators to help those suffering from severe respiratory issues. While these essential machines are still very much in demand, there is now another area in which carmakers are rallying to produce and supply into – that of personal protective equipment (PPE) for healthcare workers.
Thousands of doctors, nurses, carers and other medical staff around the world have contracted COVID-19 while tending to patients. These professionals are often referred to as the ′frontline’ when it comes to the battle against coronavirus. During times of war, factories gave themselves over to produce protective equipment for the military and they are starting to do so again for hospitals and care facilities.
For the automotive industry, the ability to manufacture PPE is easier than for others. Carmakers are able to use newly developed technologies and explore existing partnerships and supply chains, to develop equipment that can be produced quickly and delivered directly to the frontline. Alongside the modern production techniques such as 3D printing, vehicle plants also have a number of environmentally-controlled rooms to assemble certain items. At the same time, staff are already trained in the manufacturing of similar items, such as seat covers.
Therefore, at a time when togetherness and charity are key in the battle against the virus, the automotive industry can step up and help, and judging by the evidence, it is certainly doing just that.
Masking solutions
Jaguar Land Rover (JLR) is utilising its experience with 3D printing, for example, to develop visors, with an ambition to produce 5,000 a week in the UK. The business is also using facilities in Brazil to support care providers in the country with protective visors.
′We are extremely grateful to Jaguar Land Rover for their kind donation of visors to aid our frontline staff in the fight against COVID-19,’ says Glen Burley, South Warwickshire NHS Foundation Trust chief executive. ′The innovation from their designers and engineers is helping the NHS to keep our staff safe and protected, while they provide care to our patients.’
Alongside the development and production of equipment, JLR has also donated items like wraparound safety glasses, which it would usually provide to its staff.
Toyota will produce injection mould and 3D-printed medical face shields. Specifically, Toyota’s Teiho Plant in Japan is preparing to produce injection mould medical face shields with an anticipated starting production volume of 500 to 600 per week. The company is also starting to evaluate the possibility of other group companies joining in on the production. It has already started producing visors in Europe, alongside donations of PPE to medical facilities.
Supply chain
In the US, Ford is leading efforts to manufacture reusable gowns with airbag supplier Joyson Safety Systems. The project has created re-usable gowns manufactured from a material used to make airbags in Ford vehicles. Production has reached 75,000 gowns a week and will scale up to 100,000 gowns for the week of 19 April. By 4 July, the two companies say they will cut and sew 1.3 million gowns, which are self-tested to federal standards and are washable up to 50 times.
Ford worked with Beaumont Health in Metro Detroit to quickly design the gown pattern and test for sizing during fit and function trials. More than 5,000 gowns have already been delivered to the hospital.
′The need to protect our medical teams is heightened – Ford’s gown production could not come at a better time during this crisis,’ said David Claeys, president of Beaumont Health hospitals in Dearborn and Farmington Hills. ′Our front line health care workers are working around the clock to treat COVID-19 patients, and we need the necessary supplies to support them.’
Stepping up
Finally, niche Italian sports car maker Lamborghini is reconverting some departments of its production plant in Sant’Agata Bolognese to produce surgical masks and protective medical shields for the Sant’Orsola-Malpighi Hospital in Bologna.
One thousand masks a day will be made in the upholstery department, which usually produces the interiors and customisations for Lamborghini cars. At the same time, 200 protective polycarbonate medical shields will be made a day inside the composites production plant and the research and development department will assist with the use of 3D printers.
′During an emergency such as this one, we feel the need to make a concrete contribution,’ says Stefano Domenicali, chairman and CEO of Automobili Lamborghini. ′We have therefore decided to support the Sant’Orsola-Malpighi Hospital, an institution with which we have had a collaborative relationship for years, through both professional consultancy in promoting programs to protect our workers’ health, and in research projects. We will win this battle together by working in unison, supporting those who are at the forefront of fighting this pandemic every day.’