How vulnerable is global automotive production?
28 February 2024

External factors such as the recent Red Sea crisis, conflicts and component shortages can have a big impact on vehicle manufacturing. Tom Hooker, Autovista24 journalist, investigates the vulnerability of automotive production.
The performance of automotive markets, brands and individual models worldwide is connected to the fluctuation of supply and demand. This can heavily impact new-car registrations.
Without demand, manufacturers’ stock stagnates. Carmakers can respond to this by slowing the speed of production. But if supply is affected, companies may have to postpone deliveries while searching for solutions, or even worse, halt assembly lines altogether.
A dense network of automotive supply chains span the globe, providing brands with materials, components, and software. When this all runs smoothly, manufacturers can build vehicles ready for customer delivery dates.
With new vehicles made up of roughly 25,000 separate parts, just one in-car system can feature components crafted at opposite sides of the globe. This means local events can have an international impact, rattling supply chains. The recent Red Sea attacks are a primary example.
Red Sea situation
Attacks in the Red Sea have seen container ships avoiding the area, not able to take advantage of the shorter transport opportunity offered by the Suez Canal. This is a vital link for vessels travelling to Europe from Asia. The trade route enables shipping between the Mediterranean Sea and the Red Sea.
According to the World Economic Forum, the Suez Canal and Red Sea carry approximately 30% of global container traffic every year. Over one trillion dollars (€923 billion) worth of goods are moved through the area annually.
At least 33 ships in the Red Sea have been attacked by Houthi forces in Yemen, resulting in major disruption as transporters are instead sent around southern Africa. As revealed in a recent Society of Motor Manufacturers and Trades (SMMT) webinar, almost 200 vessels were reportedly diverted as of 26 January 2024.
This diversion dramatically increases shipping times. In the SMMT webinar, Kuehne+Nagel Market Intelligence estimated that re-routing around Africa is adding almost two weeks to container delivery dates.
For example, a trip from Shanghai, China to Bilbao, Spain would normally take 30 days. The current Red Sea crisis means it now takes 42 days on average.
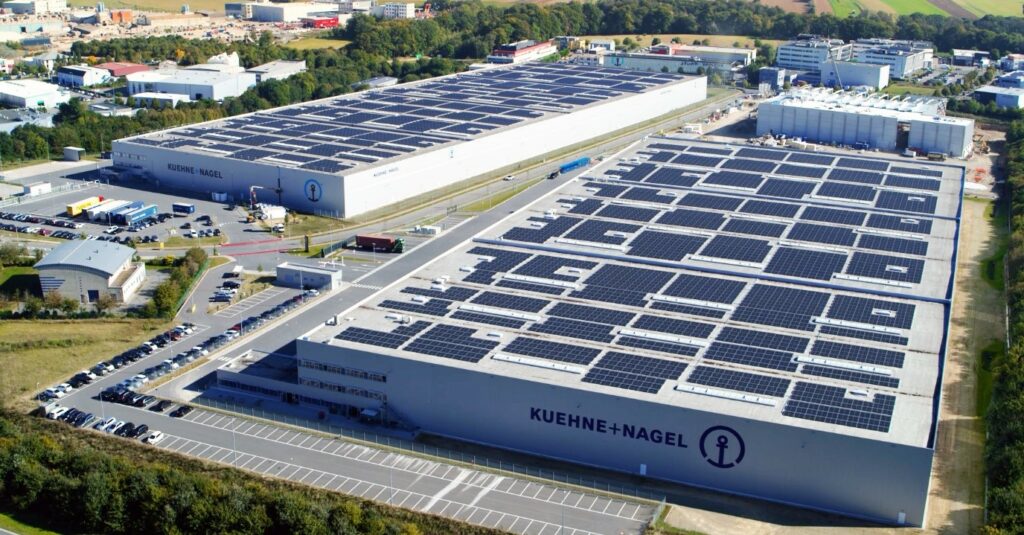
Fluid situation
‘We do not actually see any short-term change. I think what we are looking at is a situation now where carriers are reworking their networks, and [we expect] a minimum of three to six months with the situation as it is,’ explained Andrew Haggerstone, head of trade and pricing at Kuehne+Nagel.
‘The situation remains fluid and volatile. One week things can look relatively stable, the next week, not so much. So, it is really a week-by-week basis,’ Haggerstone added.
As transit times lengthened, shipping rates soared. This produced a knock-on impact for carmakers, resulting in a shortage of components coming from Asia.
Brands such as Tesla and Volvo were forced to suspend production temporarily in January. Volvo stopped work at its Belgium plant for three days, while Tesla paused output for two weeks in Germany.
Meanwhile, Volkswagen (VW) began rerouting parts around Africa last December when the attacks broke out, enabling them to account for the delay in production. Stellantis took a different approach, relying on airfreight to avoid delays.
Semiconductor shortages
While the Red Sea attacks are affecting some carmakers worse than others, the global automotive semiconductor shortage had a devastating effect on the whole industry.
With less demand during the COVID-19 pandemic, car manufacturers reduced orders for semiconductors. Meanwhile, the consumer-electronics industry needed more chips to meet increased demand from locked-down consumers purchasing laptops, TVs and gaming consoles.
However, as carmakers sought a return to normality, with production ramping back up, brands were left without a sufficient supply of chips. The semiconductor industry faced manufacturing capacity constraints and local supply chains saw disruptions such as shipping delays.
This caused delivery disruptions throughout 2021 and 2022. Automotive manufacturing was affected in turn, with temporary factory closures across Europe. This had a severe impact on automotive markets, with registrations plummeting as vehicle deliveries stalled.
Production problems
Carmakers suffered sizeable blows because of this supply bottleneck. Production at VW Group and Stellantis fell by 35% and 30% respectively. Automotive suppliers also felt the strain, as profit margins fell dramatically.
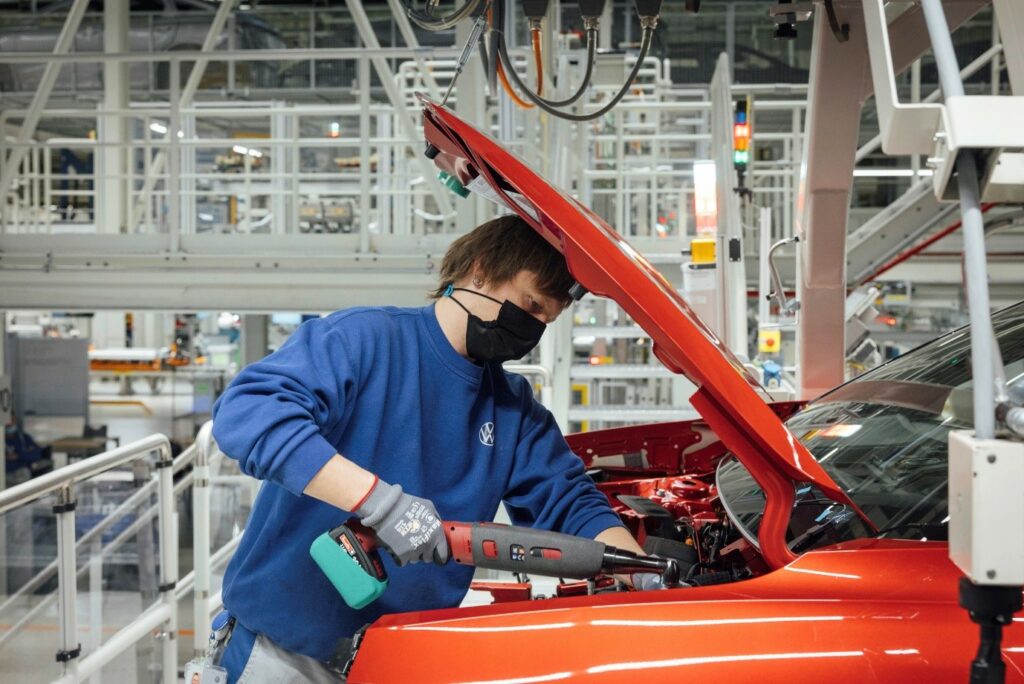
Higher new-car list prices were common during this period as carmakers passed on the additional costs to buyers. This surged in Europe from the start of 2021, meaning buyers began turning to the used-car market in greater numbers.
While the supply-chain crisis was an after-effect of COVID-19, the pandemic itself had a big impact on production lines around the world. In a 2020 report, KPMG highlighted that 78% of companies did not have enough staff to run at full production capacity. In Europe, vehicle overall production slumped by 21% on average.
Conflict complications
Russia’s invasion of Ukraine also affected supplies of key components like semiconductors and wire harnesses.
In a 2022 paper, KPMG drew attention to an estimated 400,000-unit cut in global production as a result of the conflict. Suppliers operating in the region were also affected, such as Leoni AG which makes wire systems for European carmakers.
Russia is also a major source of palladium and neon gas, used in semiconductors and catalytic converters. KPMG notes rising raw-materials costs could increase vehicle prices by up to 3% for consumers.
Component crisis
Parts shortages are still an issue, despite the semiconductor shortage mostly coming to an end. Audi stopped production for two weeks in February at its plant in Belgium, due to a lack of components.
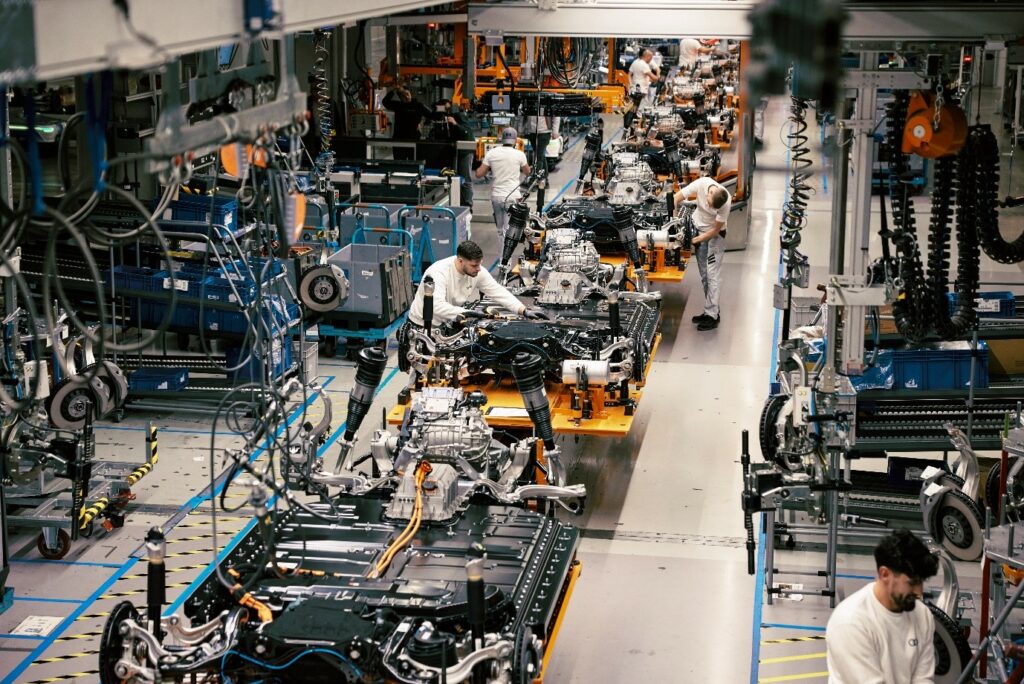
In January, Handelsblatt reported that the VW brand had to reduce its production schedule in several plants because of an electric-motor shortage.
At VW’s Emden site, production will be paused throughout March for most internal-combustion engine vehicles. This is because the plant is preparing to produce the Arteon Shooting Brake.
Striking stoppages
Strikes can also disrupt automotive supply chains. With a reduced workforce, manufacturers can struggle to maintain output levels.
Since October last year, mechanics, dockworkers and other staff have been conducting industrial action in Sweden, affecting Tesla. The dispute is supported by IF Metall, the country’s biggest union.
The strikes also spread to Denmark at the end of 2023. The nation’s largest union 3F, announced its dockworkers and drivers would stop transporting vehicles to Sweden.
Regulation effects
Production can also be disrupted by legal and regulatory changes. For example, emission rules can lead manufacturers to stop producing models if they no longer become economically or environmentally viable.
In January, Toyota said it would stop shipments of 10 models affected by certification irregularities for diesel engines. This stalled production at four plants in Japan while the matter was being resolved.
Meanwhile, the production of the VW ID.2all concept was pushed back until 2026. Citing a German media report, Automotive News Europe linked this to the relaxation of Euro 7 regulations. The electric vehicle (EV) was expected to launch in 2025.
Local solutions
While global supply chains have fed production lines in recent times, there is now increased motivation for localisation in the wake of international logistical disruption.
Stellantis has invested in a French sodium-ion battery maker to help it produce affordable EVs in the future. This means it will be able to reduce its reliance on shipped units.
Alongside this, the carmaker looks to benefit from a joint venture with Mercedes-Benz and TotalEnergies. The trio plans to build three gigafactories across France, Germany and Italy.
Chinese brands face a different problem. While currently leading the battery technology race, manufacturers such as SAIC are dependent on shipping operators to expand into Europe.
However, there are opportunities to expand into the logistics market, enabling better control over supply lines. In January, SAIC launched its own cargo ship, the SAIC Anji Logistics. With an annual capacity of 30,000 vehicles, the vessel will transport models to Europe.
BYD is taking the same approach, its BYD Explorer No.1 set sail for Europe with more than 5,000 EVs on board. The brand is also attempting to create an integrated supply chain, holding talks with a lithium producer in Brazil.