Larger gigafactories mean lower production emissions
11 February 2022
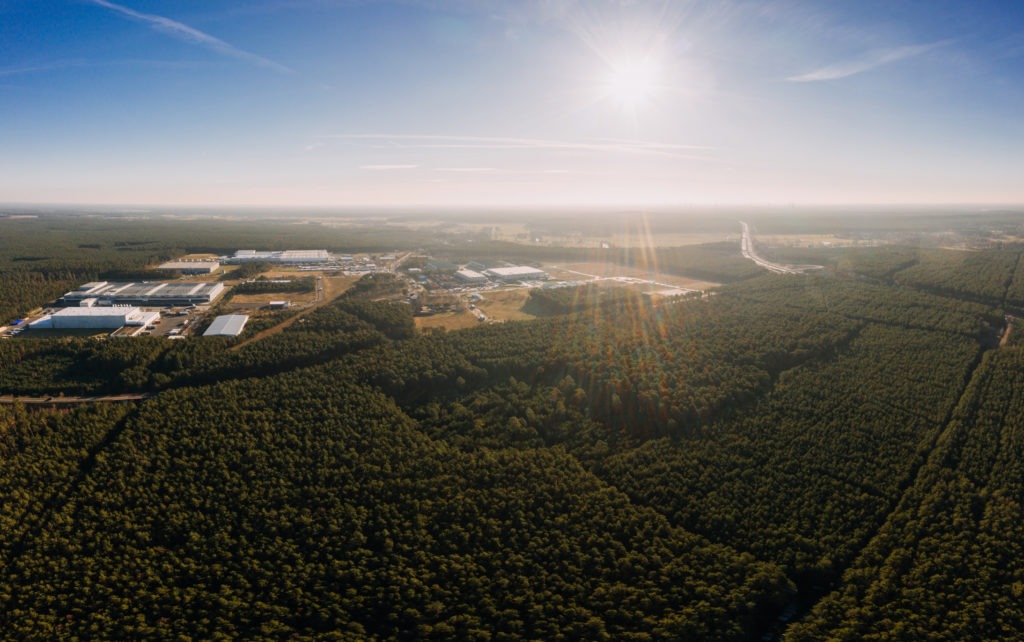
The automotive industry is undergoing two simultaneous transitions: electric and environmental. Electrically-chargeable vehicles (EVs) are considered a greener option than internal-combustion engines (ICE). However, the necessary battery production has drawn the ire of sceptics who point to the creation of emissions.
But scaling up manufacturing through ‘enormous gigafactories’ can cut the environmental impact significantly compared with smaller-scale manufacturing, according to new research from Chalmers University of Technology in Sweden. The study shows that carbon emissions can even be reduced to roughly one quarter when factories use green electricity.
Bigger is better
Many pundits ask the question, are EVs as green as they seem? A determining factor in this discussion is the manufacture of battery cells, which store electricity to power the motors. Research in the last decade has examined just how the creation of these essential components impacts the environment. However, the data used often focuses on small-scale production or even pilot projects.
But Mudit Chordia, doctoral student and lead author of the new Chalmers study, points out that production capacity is scaling up massively. Unfortunately, there is little data on how this growth will affect emissions, which leaves research and reality at odds. To address this, researchers used a life-cycle assessment to remodel a commonly-cited small-scale production study. This was then combined with updated data, which more closely represents modern facilities.
‘Our results revealed how upscaling battery production from megawatt to the gigawatt level yields significant reductions in energy usage per kilowatt-hour of battery-storage capacity produced – up to 58%. The efficiency gains of large-scale production are highly significant,’ Chordia said.
When adjusting for different energy supplies, even in the most carbon-intensive South Korean case, emissions were observed to drop by nearly 45%. If low-carbon power was sourced, emissions fell by a further 55%. So, in low-carbon electricity countries like Sweden, where Europe’s largest battery factory is currently being built, the potential for green battery production is very good.
Supply-chain shift
The study also points out that large-scale production is pushing a greater proportion of impact up the supply-chain. Most crucially, the raw material extraction and processing phases. One challenge faced by researchers was getting access to the necessary data to model this process and analyse the environmental impacts.
‘In the course of our work, we found that life-cycle assessment datasets, often used for some of the battery raw materials, lack the coverage and precision necessary for modelling the high grade of material quality required in battery production,’ said Anders Nordelöf, researcher and co-author of the study.
Manufacturing supply chains are usually considered trade secrets, making it very challenging to collect all the necessary data. Nordelöf explained that a focused effort on procuring raw materials from low-carbon intensity mineral extraction is needed if the environmental impacts of battery production are to be further reduced. ‘But in such a competitive industry, this will remain a challenge for many actors,’ he added. More companies are entering the battery gold rush every day. From mining to processing and development to production, this competition will only continue to rise alongside increasing demand.