Electric-vehicle gigafactories planned in Sweden, France, and Germany
07 February 2022
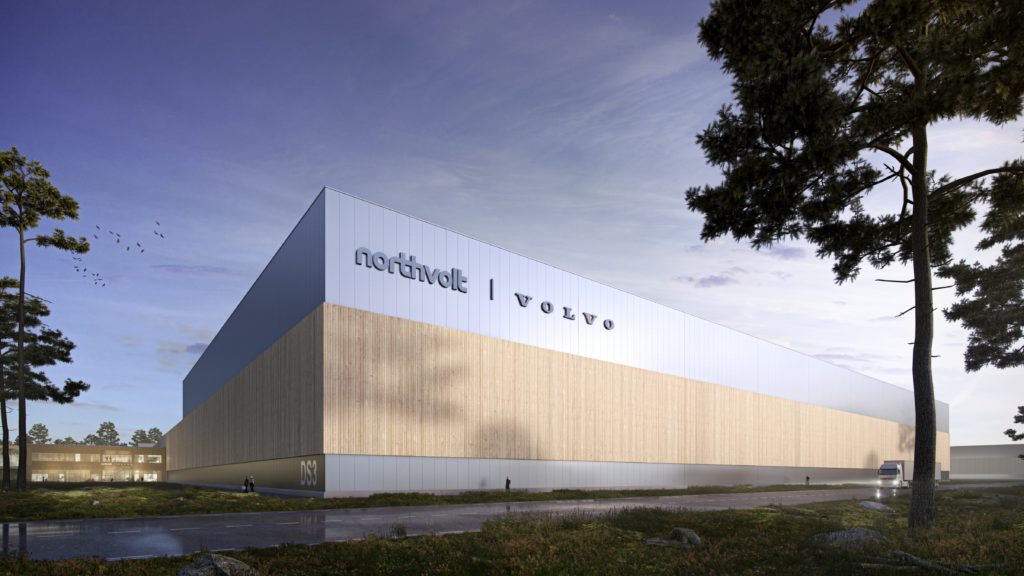
Europe is looking inward for battery-building bases. Volvo’s goal is a Gothenburg gigafactory in Sweden, Verkor will develop in Dunkirk, France, and Rock Tech Lithium will work with Bilfinger in Brandenburg, Germany. These plans illustrate three prominent automotive megatrends: electromobility, sustainability, and supply-chain shortages.
But instead of taking place in isolation, their influence has an interwoven lattice effect. As more electric models hit the market, there is an increasing need for batteries. But these components must be produced in an environmentally-conscious manner to ensure electromobility can hold on to its green credentials. This is encouraging the localisation of production, lowering shipping emissions as well as the damaging effect of parts shortages.
Gothenburg gigafactory
In 2025, Volvo and Northvolt will open a battery-manufacturing plant in Gothenburg, Sweden, following two years of construction. It will produce state-of-the-art cells, specifically developed for use in the next generation of all-electric Volvo and Polestar models. With a potential annual production capacity of 50GWh, the Gothenburg site could supply batteries for roughly half a million cars a year. As the carmaker plans to go electric-only by 2030, this capacity will be essential.
‘Our battery-cell partnership with Northvolt is key to our strategic ambitions in electrification,’ said Håkan Samuelsson, Volvo Cars chief executive. ‘We are committed to becoming a leader in the premium-electric-car segment and selling only pure-electric vehicles by 2030.’
Creating 3,000 new jobs, the gigafactory will work alongside an R&D centre announced in December last year as part of a SEK 30 billion investment (€2.8 billion). It will also benefit from a direct route to Volvo’s largest car plant, access to infrastructure, and a pipeline of renewable energy. The battery-cell facility will be powered by fossil-free energy, while also integrating circular and efficient solutions.
‘Our new battery plant will support our ambition to have a fully climate-neutral manufacturing network and secure a supply of high-quality batteries for years to come,’ said Javier Varela, head of engineering and operations at Volvo Cars. ‘Through our partnership with Northvolt, we will also benefit greatly from an end-to-end battery value chain, from raw material to complete car, ensuring optimal integration.’
Dunkirk development
French industrial company Verkor also announced the construction of a new gigafactory, this time in Dunkirk, France. Designed to support Europe’s net-zero goals, this site will manufacture low-carbon battery cells for electrically-chargeable vehicles (EVs). With construction scheduled for 2023, the first unit deliveries look to commence in July 2025.
‘We are eager now to work with our partners to unite all the winning conditions to build the best battery-cell factory in the world,’ said Benoit Lemaignan, CEO of Verkor. ‘Dunkirk is the best choice among many other great opportunities, and I really want to thank all the people in the territories, as well as our partners including Groupe IDEC, who supported us in this process.’
Beating out roughly 40 other potential locations across France, Spain, and Italy, the upcoming Dunkirk site will cover some 150 hectares. Up to 1,200 direct jobs and over 3,000 indirect jobs are expected to be created in the first phase of the project. Once up and running, the gigafactory will begin supplying several customers including Renault Group in line with a strategic partnership that was signed last summer.
‘Mastering the entire battery value-chain is critical to the transition to electric mobility. I welcome this new important step by Verkor. Their choice of location reinforces “the electric battery valley” that is taking shape in the Hauts de France, as well as its dynamic ecosystem,’ said Agnès Pannier-Runacher, the French minister of industry. ‘It sends a positive signal to Dunkirk’s industrial platform, which has key assets in the sector. Verkor, like many players in the value chain, can rely on the government’s ongoing support under the France 2030 plan.’
Bilfinger in Brandenburg
Elsewhere, industrial service provider Bilfinger will act as engineering, procurement, and construction manager (EPCM) for clean-tech company Rock Tech Lithium. The arrangement covers the building of Europe’s first lithium-hydroxide converter in Brandenburg, Germany. Currently, in the advance-planning stage, the plant is set to produce 24,000 metric tonnes of lithium hydroxide annually for the batteries of 500,000 EVs.
‘The production of lithium-hydroxide as a component of electric-car batteries is essential for a climate-friendly mobility transition,’ said Christina Johansson, interim CEO and CFO of Bilfinger. ‘The concept developed by Rock Tech Lithium for the construction of the lithium-refining plant is innovative and technologically convincing.’
Rock Tech Lithium wants to produce lithium-hydroxide across the whole value chain, while also having the lowest-possible environmental impact. Working with the German Lithium Institute ITEL, the company has developed a zero-waste strategy. This includes recycling the by-products of lithium-hydroxide production, with the aim of recycling the lithium itself at a later stage.
‘The cooperation is another significant milestone for Rock Tech Lithium on its way to becoming a leading clean-tech company supplying the automotive industry with high-purity lithium hydroxide,’ said Markus Brügmann, CEO of Rock Tech Lithium. ‘Together with Bilfinger, we want to drive the battery era forward.’