BMW’s Munich plant rolls out new i4 BEV after upgrade
27 October 2021
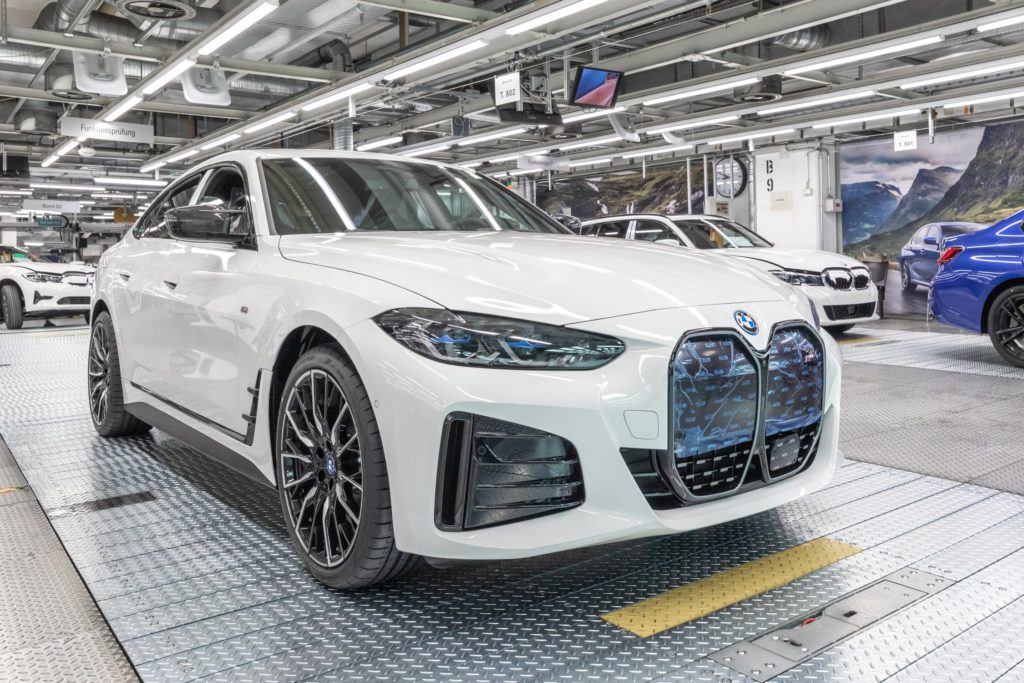
The first BMW i4, a performance battery-electric vehicle (BEV) from the carmaker’s M division, has begun rolling out of Munich. This means the carmaker’s home plant now builds all drivetrain types along a single line. This moment signifies an important transition for BMW, as it works towards its electrification targets.
‘For the plant and team, the launch of the BMW i4 is a milestone on the road to electric mobility,’ said Milan Nedeljković, BMW Group board member for production. ‘By 2023, more than half of all vehicles from our Munich facility will have an electrified drive. The majority will be fully electric. So, Munich goes fully electric.’
Alongside the i4, the Munich site currently builds a range of other vehicles. This includes the internal-combustion engine (ICE) and hybrid 3-Series sedan and touring models. Additionally, there is the M3 and the 4 Series Gran Coupé.
A challenging process
The nearly 100-year-old plant required a €200 million upgrade to produce the i4. The carmaker admitted converting and installing new systems proved particularly challenging, with space constraints a notable hurdle. However, all of this was achieved without halting production.
Peter Weber, director of BMW Group’s Munich plant, highlighted the modern technology now at play. ‘Our body shop is a shining example of intelligent, efficient integration. Most of the new production processes for the BMW i4 can be carried out on the existing body-shop systems,’ he explained.
BMW first announced plans to invest €400 million in the plant’s assembly capabilities less than a year ago. A roadmap was laid out to construct new assembly and body-shop sites elsewhere to free up Munich. By the end of this year, four-cylinder engine production will have moved to Hams Hall in the UK, and Steyr in Austria. The total relocation of engine manufacturing from Munich should be completed by 2024 at the latest.
Integrating electromobility
The electric drive and battery are the two stand-out components when comparing the construction of a BEV, like the i4, to an ICE architecture. But this meant that roughly 90% of Munich’s existing body shop could still be used for other elements of BEV building. Additional systems were only required for the floor assembly and rear end.
Integrating the battery into the production line was a complex task. The essential unit is now bolted onto the body by an automated assembly system that works from below the vehicle. High-resolution cameras scan the body before mounting to ensure its surface is clean with no impurities that could cause damage.
3D scanning
The Munich plant is being 3D scanned in minute detail. This will provide a set of digital data of both the building and its systems. These scans are then processed and saved onto the cloud, meaning the data can be accessed anywhere, at any time on a browser.
Several plants, including Spartanburg and Regensburg, have already undergone this process. Dingolfing is also undergoing 3D scanning. By the end of next year, all major BMW Group plants will have been scanned. But what can data like this actually be used for?
Virtual planning tools are already used by the manufacturer to develop buildings and systems. For example, axle pre-assembly for the i4 was planned with Nvidia’s Omniverse Nucleus platform. This software allows data from different design and planning tools to be merged, producing a photorealistic, real-time simulation within a collaborative environment. Other applications include radio frequency identification (RFID), which means parts can be identified and assigned automatically along the value chain.
Environmental evolution
Between 2006 and 2020, resource consumption per car produced fell more than half, and CO2 emissions dropped by 78%. But BMW wants to reduce the emissions per vehicle by another 80% by 2030. Munich has already made some changes in this vein.
For example, the plant now uses reverse osmosis to cut freshwater consumption. Integrated in spring this year, this system treats water from the cathodic dip – where base coats are applied to vehicles – so it can be re-used. This process is expected to reduce annual freshwater consumption by more than six million litres.
The carmaker also wants to make greater use of railways and battery-electric trucks to help lower local emissions from transport and logistics at its Munich plant to zero. 750 trucks are currently needed every day to deliver parts, and the company wants inner-city journeys to be made by BEVs. Additionally, the number of vehicles leaving Munich by train will increase from the current 50%.
‘We are well aware that, owing to the city location of our production facility, we have a special responsibility,’ said Weber. ‘Our project to reduce CO2 emissions at our home plant will have a major impact that is positive both for the environment and for our immediate neighbourhood.’