Fossil-free steel will help lower Volvo’s carbon footprint
18 June 2021
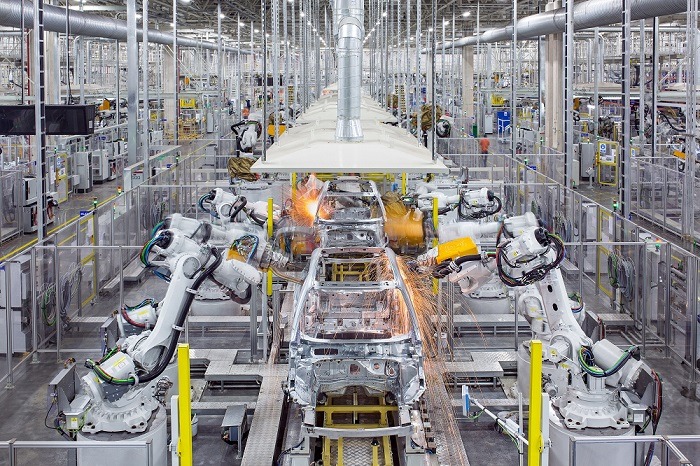
Volvo Cars (Volvo) is partnering with Swedish steelmaker SSAB to explore the development of automotive-grade materials manufactured without fossil fuels.
The carmaker is the first to collaborate with SSAB and will work with the steel company and its HYBRIT initiative, an ambitious project in fossil-free steel development. The move adds more credibility to Volvo’s plans to be a carbon-neutral company.
HYBRIT was started by SSAB, iron-ore producer LKAB, and energy firm Vattenfall. It aims to replace coking coal, traditionally needed for iron-ore-based steelmaking, with fossil-free electricity and hydrogen. The result is expected to be the world’s first fossil-free steelmaking technology, with virtually no carbon footprint.
As part of the agreement, Volvo will be the first automotive business to secure a supply of steel made from hydrogen-reduced iron – from HYBRIT’s pilot plant in Luleå, Sweden. This supply will be used for testing purposes, and Volvo may use some of the product in a future concept car.
As the steel is being produced using new production techniques, it makes sense for Volvo to ensure its safety for vehicle use before mass production. The testing will also give the Swedish carmaker a chance to evaluate how the production process of the steel needs to be stepped up for automotive manufacturing.
Fossil-free
In 2026, SSAB aims to supply the market with fossil-free steel on a commercial scale. Therefore, Volvo aims also to be the first carmaker to use fossil-free steel for its own production cars.
‘As we continuously reduce our total carbon footprint, we know that steel is a major area for further progress,’ said Håkan Samuelsson, chief executive at Volvo Cars. ‘The collaboration with SSAB on fossil-free steel development could give significant emission reductions in our supply chain.’
The global steel industry accounts for around 7% of direct-carbon emissions worldwide, according to Volvo. This is because the industry is currently dominated by iron-ore-based steel-making technology, using blast furnaces depending on coking coal.
SSAB aims to reduce Sweden’s CO2 emissions by 10%, and those in Finland by 7%, through the HYBRIT technology, using hydrogen produced from water and fossil-free electricity instead of coking coal.
Carbon footsteps
The CO2 emissions related to steel and iron production for Volvo cars amounts to around 35% in an internal-combustion engine model, and 20% in a battery-electric vehicle (BEV), of the total CO2 emissions from the material and production of components.
Volvo has already announced that it will become a BEV-only company by 2030. However, as the figures above suggest, this will not drastically reduce their overall carbon footprint. This is because the carmaker’s decarbonisation plan also seeks to tackle carbon emissions in the company’s wider operations, supply chain, and recycling and reuse of materials.
In the short term, these and other steps aim to reduce the life-cycle carbon footprint per car by 40% between 2018 and 2025. Furthermore, by 2040, Volvo’s ambition is to be a climate-neutral company. Therefore, the partnership with SSAB is a strong step in the right direction towards these goals.
‘We are building an entirely fossil-free value chain all the way to the end customer,’ added Martin Lindqvist, president and CEO at SSAB. ‘Our breakthrough technology has virtually no carbon footprint and will help strengthen our customer´s competitiveness. Together with Volvo Cars, we aim to develop fossil-free steel products for the cars of the future.’