Northvolt and Daimler commit to battery recycling
18 November 2021
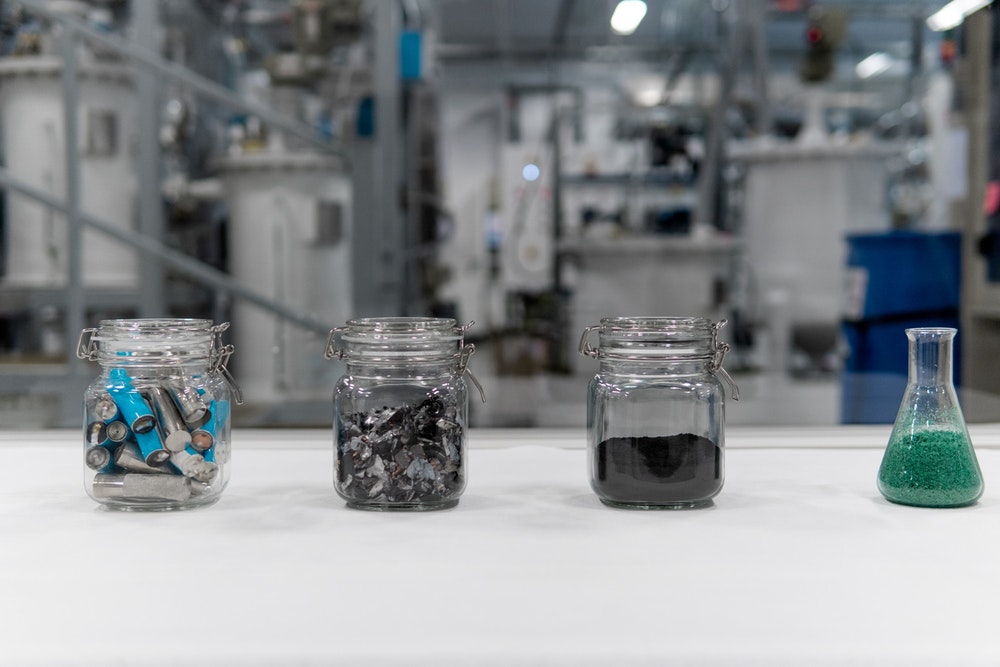
The EU aims to have at least 30 million electrically-chargeable vehicles (EVs) on its roads by 2030. While these do not emit carbon dioxide, there have been concerns about the lifecycle of batteries found in electric cars.
Automotive and energy companies have stepped up their efforts when it comes to battery recycling. Swedish startup Northvolt announced it had produced its first fully-recycled battery cell this week. Marked as a milestone for the company, it is yet another example of firms setting new benchmarks for sustainability in manufacturing.
Northvolt, co-founded by former Tesla manager Peter Carlsson, said the battery cell is made with 100% recycled nickel, manganese and cobalt. It intends to ramp up its recycling facilities in Sweden, aiming to expand its plant capacity there to enable the recycling of 125,000 tonnes of batteries per year. This is no small figure and amounts to around 30GWh of battery production per year.
Breakthrough for battery industry
Northvolt’s news signals another breakthrough for the battery industry as creating a sustainable supply chain is key to supporting decarbonisation.
‘What we have shown here is a clear pathway to closing the loop on batteries and that there exists a sustainable, environmentally-preferable alternative to conventional mining in order to source raw materials for battery production,’ said Emma Nehrenheim, Northvolt’s chief environmental officer.
As the transition to electromobility gains speed, companies are facing the obstacles of how to deal with spent EV batteries. 250,000 tonnes of batteries will reach their end-of-life in Europe by 2030. Looking at novel ways to cut e-waste will be crucial in making the supply chain more sustainable.
Hence, treating end-of-life batteries as a valuable product and not a waste material sounds promising. Circularity is destined to play a major role in the near future, significantly reducing the environmental impact of the battery industry.
Recovering 95% of metals
‘The recycling process can recover up to 95% of the metals in a battery to a level of purity on par with fresh virgin material. What we need now is to scale-up recycling capacities in anticipation of future volumes of batteries requiring recycling,’ added Nehrenheim.
Having proven the potential of recycled material, the Swedish company aims to produce cells with 50% recycled material by 2030. Its first giga-scale recycling plant is expected to start operations in 2023, with the intention of becoming Europe’s largest battery-recycling plant.
Northvolt said the large-scale facility will be one of a kind in Europe as it will be capable of recycling lithium in addition to nickel, manganese, cobalt and other metals. Recovered materials from the site will supply Northvolt’s gigafactory with recycled metals sufficient for 30GWh of battery production per year.
The battery-production process does not end there though as the recycling plant will also be able to recover copper, aluminium and plastics from the batteries and materials it recycles. These will be recirculated into manufacturing through local third parties.
Daimler’s recycling plant
Daimler’s Mercedes-Benz is one of the carmakers keen on electrifying its fleet as it prepares to go all-electric by the end of the decade, at least where market conditions allow. At a recent conference hosted by German newspaper Handelsblatt, CEO Ola Källeniussaid the manufacturer was planning to build a recycling factory although he did not provide further details.
When contacted by Autovista24, Mercedes-Benz confirmed the plans and said: ‘In order to sound out the best technologies and to be able to fully implement the idea of a circular economy, we are currently examining the construction of a new pilot factory for recycling lithium-ion battery systems at the Kuppenheim [Germany] location.’
‘The start of the factory is planned for 2023, depending on the promising talks with the public sector. The aim is to present a holistic and sustainable recycling approach for lithium-ion batteries. This should set standards from both ecological and economic points of view and enable maximum recovery rates through an innovative process design: a real recycling economy for battery materials,’ it added.
Daimler wants to gradually increase the proportion of recycled parts in its cars. Back in July, Mercedes-Benz announced plans to set up eight factories for producing battery cells in addition to nine plants dedicated to building battery systems. The manufacturer is also in talks with partners to develop batteries with a particularly high energy density and safety.