BMW to use sustainable aluminium wheels to cut carbon emissions
13 April 2022
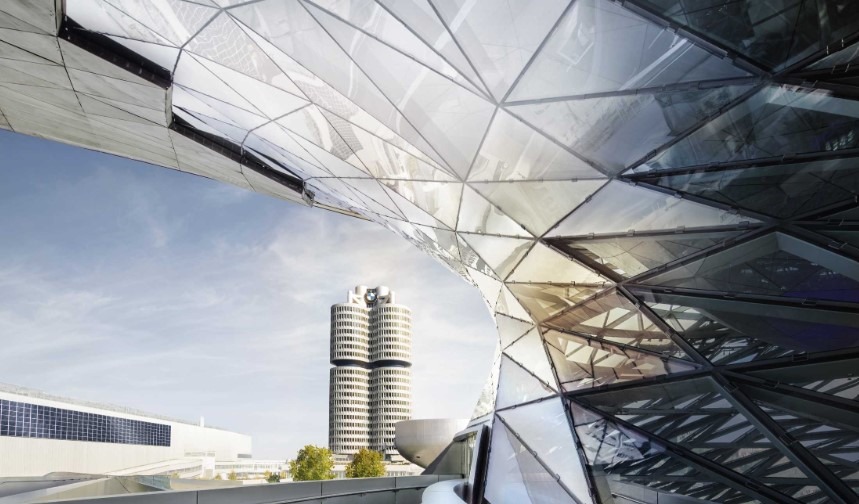
As BMW wants to be the most sustainable carmaker in the world, the group now plans to use more environmentally-friendly aluminium wheels from 2024 across its brands. Produced with 100% green energy, the wheels will save up to 500,000 tonnes of CO2 per year – this is not a small amount, given wheel production at BMW makes up 5% of carbon emissions from supply chains.
The Munich-based manufacturer said more sustainable car components will slash these emissions by more than 50%. The company has signed agreements with all its wheel suppliers to make the transition happen.
‘Green power is one of the biggest levers for reducing CO2 emissions in our supply chain,’ said Joachim Post, BMW board member, who is responsible for the purchasing and supplier network. ‘We have already signed more than 400 contracts with our suppliers, including suppliers of car wheels and aluminium, requiring them to use green power.’
Good recycling properties
Aluminium alloy car wheels are energy-intensive to produce. They account for up to 12% of the total CO2 emissions in a wheel’s lifecycle, according to one of the automotive industry’s biggest suppliers, Maxion Wheels, which counts BMW among its customers.
From 2023, Mini will start using light-alloy cast wheels made from 70% secondary aluminium in the new Countryman. By using both renewable energy and secondary raw materials during car manufacturing, carbon emissions can be lowered by up to 80%, BMW said.
Like steel, aluminium has beneficial recycling properties, which makes it a good candidate for BMW’s circular economy strategies. The lightweight metal can be used as a secondary raw material since it is relatively easy to melt down old wheel parts. This then removes the need for energy-intensive processes to produce the primary raw material.
Greener automotive supply
Making automotive supply chains more sustainable is one of the greatest challenges carmakers face. Reusing recycled materials is a key approach to making car manufacturing greener. BMW plans to bring a fully-recyclable car to the market by 2040, which bets on secondary aluminium.
Since last year, BMW has sourced aluminium from the United Arab Emirates, where the metal is being manufactured using solar-powered electricity. The carmaker then processes the aluminium in Bavaria to make body and drivetrain components.
To increase sustainability in the supplier network, BMW is part of several projects to standardise raw-material extraction, including the Aluminium Stewardship Initiative (ASI). Many of its wheel suppliers have joined the initiative, committing to the responsible use of aluminium.
By the end of the decade, BMW targets to cut emissions throughout the supply chain by 20%. Steel, which is highly emission-intensive to produce, is also on the list of materials the carmaker wants to make more sustainable. It recently inked a deal with one of Europe’s largest steelmakers, Salzgitter AG, to source low-carbon steel from 2025.
In a push to decrease vehicle emissions embedded in interior materials, BMW is eager to use more sustainably-sourced products. Earlier this month, it announced an investment in green-material company Bcomp, which produces sustainable materials from bio-based sources, such as flax fibres.