The race to secure Europe’s EV battery supply chain
16 November 2022
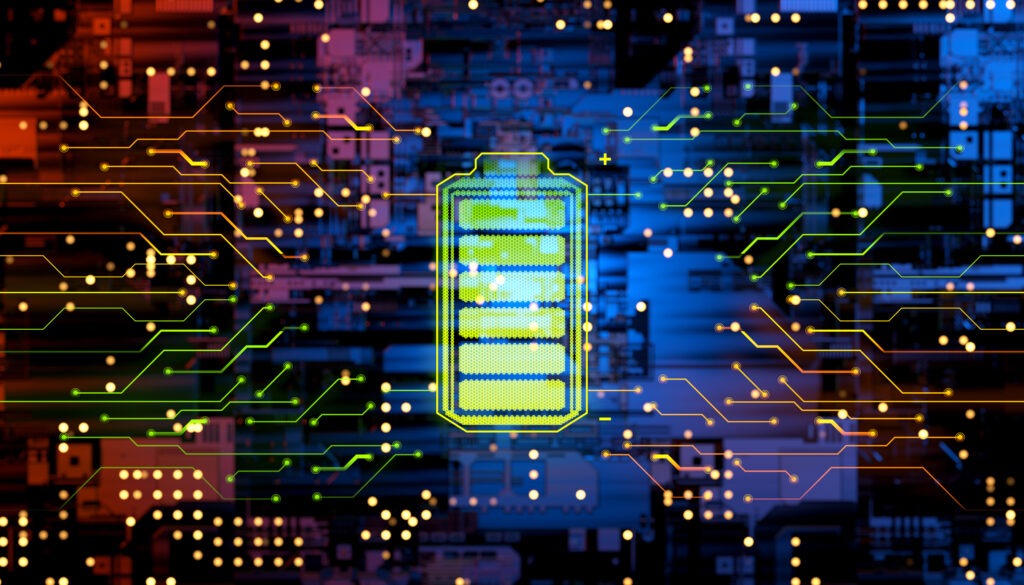
Supply chains for electric-vehicle (EV) batteries remain constrained as the industry shifts to electromobility. Philipp Seidel, principal at Arthur D. Little’s Munich office, highlights risks and opportunities for the automotive industry in an interview with Autovista24 journalist Rebeka Shaid.
Supply chains have seen disruptions since the COVID-19 pandemic, and the past months have proved to be particularly challenging as carmakers are scrambling for raw materials to produce enough EV batteries. The tense geopolitical environment, fuelled by the war in Ukraine and growing friction with China, as well as rising costs are taking a toll on manufacturers and suppliers.
Seidel, who co-authored a recent piece about the EV battery supply chain, highlighted that demand for EV batteries and materials exploded and will continue to grow by around 30% annually over the next years, not least in Europe. Carmakers such as Volkswagen (VW) Group are planning to build several gigafactories in Europe as they ramp up EV manufacturing. Governments are also subsidising battery projects across the continent in the hope to decrease dependence on foreign markets, such as China.
‘A big portion of the battery supply chain is happening in China, South America, South East Asia or other remote parts of the world. But Europe wants to become less dependent on these markets in the future,’ said Seidel. ‘The Chinese have been ahead of Europe for a decade, and Europe needs to catch up now.’
Complex set-up
This could prove to be a complicated affair. Seidel believes that Europe cannot build a fully independent supply chain for EV batteries because it does not have the natural resources for the raw materials.
‘We will continuously have to import materials to produce batteries here. The European industry will not be fully viable without those remote parts of the supply chain, but we should aim for more balance and resilience in our sources,’ he said.
There is added complexity because the EV-battery supply chain operates on a global scale. ‘We have mining operations in South America and in Australia. We have processing of materials in China. And then we have the application to actual battery cells either in China or North America and Europe. A lot of companies from a lot of industries are involved,’ Seidel explained.
This, he added, makes aligned and coordinated investments according to demand difficult. There are many steps involved in producing an EV battery pack. While European companies, such as Sweden’s Northvolt, aim to shift more value creation to Europe, Asian players will continue to play important roles in upstream parts of the value chain.
‘We are not only seeing European companies set up [operations] in the battery supply chain in Europe, but we also have Chinese and Asian companies with European operations.’
The world’s leading battery supplier, China’s CATL, is in the middle of setting up an EV battery plant in Germany and is planning to build a second European factory in Hungary. It has also been rumoured that Chinese EV maker BYD, which has recently entered the European market, is thinking about localising production on the continent.
Sustainability
While European carmakers keep leaning on Asia to build EV batteries – even on home turf – Seidel emphasised another factor that is adding pressure to the supply chain: sustainability. He explained that, on one hand, greater awareness of climate change is driving demand for EV batteries and clean energy.
‘But on the other hand, it puts pressure on how batteries are produced, and from which materials. Most battery raw materials are either mined or processed in China. Given the energy mix of the country, you can imagine that those materials come to battery factories with a huge CO2 footprint, which starts to become a problem,’ he said.
One approach to improve sustainability and autonomy in Europe is battery recycling. ‘We need to set up recycling of batteries to keep the materials, which have reached Europe, in the loop to recirculate them into the supply chain after their first life in a battery. Only then are battery-electric vehicles truly sustainable,’ Seidel said.
Europe’s automotive industry has recognised the need to roll out battery-recycling facilities. Pilot projects are currently in the works, including one from Mercedes-Benz, which wants to recycle more than 96% of a spent EV battery in the future.
Projects like these will be crucial to ensure greater responsibility and sustainability when it comes to making automotive supply chains more ethical. ‘To minimise the use of natural resources, it does not make sense to transport huge, heavy and potentially hazardous batteries around the globe,’ Seidel said.
The lifecycle assessment for EVs with batteries produced in China has a CO2 footprint from the production phase that is 30% to 40% bigger than the footprint of a fossil fuel-powered car, he added. And since the battery emits the most CO2 during the production phase, bringing those emissions down can contribute to the overall sustainability of electric vehicles.
Economical and technology risks
The current energy crisis that is sweeping Europe poses another challenge, both to battery production and EV adoption. With power prices surging, consumers could get wary of acquiring an electric car. At the same time, manufacturers and automotive suppliers are hit with higher costs.
Northvolt has already hinted at possibly delaying the construction of its German gigafactory. Chemical giants, such as BASF, are heavily dependent on gas as an energy source and with costs rising, these companies may encounter issues processing battery materials and intermediate products to supply the growing EV industry, said Seidel.
‘The energy crisis makes industrial battery production in Europe more expensive and more difficult. This hurts the new emerging and energy-intensive battery industry, which is just trying to set up in Europe,’ added Seidel.
But he pointed out that the energy crisis could also present the European industry with unique opportunities. ‘It gives Europe a good argument to set up operations in Europe because we tend to have more renewables than China. And we can produce batteries with cleaner energy,’ he said.
Battery-cell producers are facing more financial risks during production ramp-up because of huge capital requirements. There are also technological perils as the production of an EV battery pack can lead to huge monetary losses during the first years of manufacturing. And companies have to handle vast amounts of battery scrap that, again, needs to be recycled.
Additionally, battery technology itself can pose a problem, with companies having to carefully consider their investment and payback periods. ‘If you set up battery production now and invest billions in in the production line for a certain type of battery, there is a high probability that this battery is no longer state-of-the art in 10 years’ time,’ said Seidel.
Shifting attitudes
So, how can the EV battery supply chain become more resilient? The good news is that automotive players are changing the way they operate and secure supplies of critical battery materials. In the past, car manufacturers were primarily in contact with their direct suppliers. But now, the focus has shifted to what is happening upstream.
More manufacturers are signing long-term agreements with material and chemical companies to gain greater control over the supply chain. This also helps to increase understanding and transparency about how supply networks operate.
Seidel said that automotive manufacturers are stepping out of their usual roles and are now working closely with tier two and tier three suppliers, such as raw-material providers.
‘The challenges of the battery supply chain can only be addressed with a more coordinated, more integrated end-to end approach and this is something new, at least to most automotive manufacturers,’ Seidel concluded.