How can electric-vehicle batteries become more sustainable?
23 March 2022
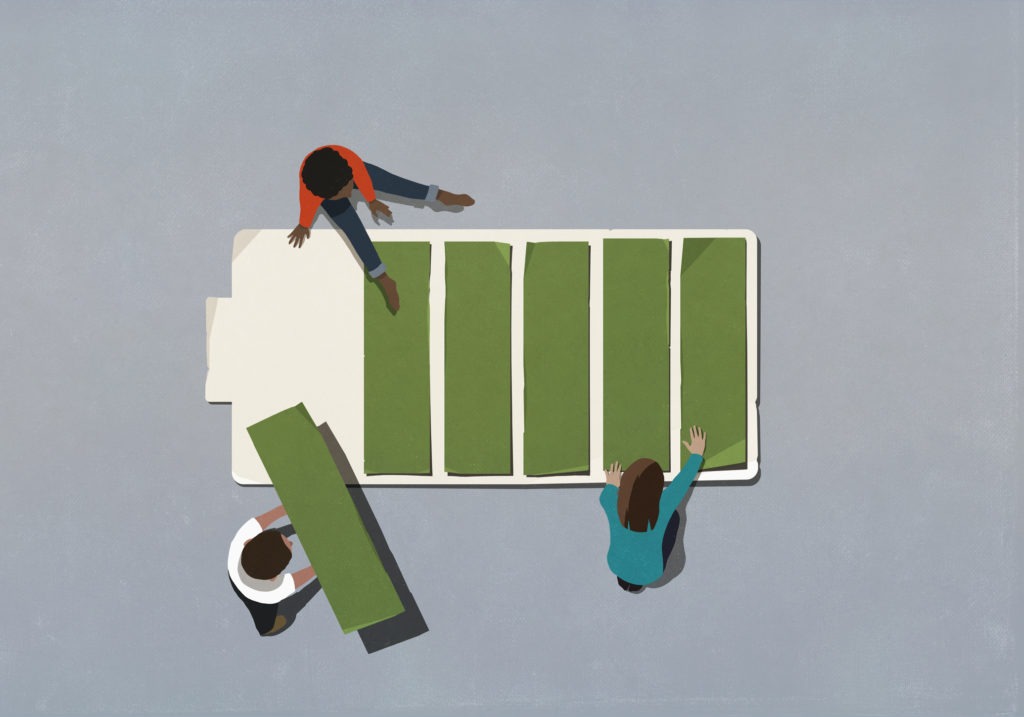
Electromobility and sustainability are two intertwined megatrends reshaping the automotive industry. However, electric-vehicle (EV) batteries are still a major source of emissions. Autovista24 editor Phil Curry, deputy editor Tom Geggus, and journalist Rebeka Shaid discuss how carmakers, suppliers, technology companies and governments are transforming the essential electric component.
You can listen and subscribe to receive podcasts direct to your mobile device, or browse through previous episodes, on Apple, Spotify, Google Podcasts and search for Autovista24 Podcast on Amazon Music.
Show notes
MB: Mercedes-Benz establishes sustainable battery recycling: Own recycling plant to start in 2023
VW: Volkswagen Group on course for New Auto: deliveries of battery-electric vehicles doubled in 2021
BMW: From raw material to recycling: BMW Group develops sustainable material cycle for battery cells
VW: Volkswagen Group joins the Initiative for Responsible Mining Assurance
Northvolt to open third EV-battery gigafactory in Germany
VW secures lithium supply in deal with Vulcan Energy
ECCUC: Sustainable batteries: member states ready to start negotiations with Parliament
Podcast synopsis
The automotive industry cannot achieve sustainability along its supply chains without looking at the most emission-intensive part of an EV – the battery.
While electric vehicle batteries are complex to dismantle once they reach the end of their lifecycles, carmakers are trying to save them from ending up in landfills through recycling. This allows automotive companies to not only save costs, but also retrieve valuable rare-earth materials, such as lithium, cobalt, and nickel. Big German vehicle manufacturers – Mercedes-Benz, Volkswagen (VW) Group, and BMW – are all eager to ramp up battery recycling in their own pilot plants, aiming to achieve recycling rates of more than 90%.
Promising Swedish startup Northvolt is working on producing the world’s ‘greenest’ batteries, made in Europe, to supply automotive companies including Volvo, VW, Polestar, BMW, and Scania. Meanwhile, German-Australian lithium developer Vulcan Energy is working on a zero-carbon project to extract lithium to supply the European EV industry. Combined, these efforts will help support Europe’s mission to make mobility more sustainable and circular.
Recharging regulations
While vehicle manufacturers work to build more sustainable EV batteries, governments are also looking to enforce greener EV development. The European Council is currently working on a set of new rules to establish sustainability and safety throughout the battery supply chain and life cycle.
‘Batteries are a key element of the clean energy transition. The new rules will promote the competitiveness of European industry and production chains and make more batteries available for our shift towards zero-emission modes of transport,’ said Barbara Pompili, minister for ecological transition.
‘The new rules will ensure end-of-life batteries will be properly collected and will not end up discarded in the environment. This will prevent toxic substances contained in them from being released in the environment and drastically limit the wasting of precious materials that could be recovered in the context of a circular economy.’
Alongside this, companies are deploying blockchain to ensure the sustainable sourcing of batteries. The decentralised ledger technology makes the history of a digital asset unalterable and transparent through decentralisation and cryptography.
Securing automotive supply chains
Sustainable EV batteries are nothing without a good supply chain in place. Materials need to come from reputable sources, manufacturing needs to take place in specially created gigafactories, and finished batteries need to be shipped to carmakers’ manufacturing plants ‘just-in-time’ for assembly into the vehicle.
However, the longer the supply chain, the harder it is to ensure sustainability. This is why many carmakers are building gigafactories in Europe, rather than continuing to rely on supplies from Asia. Long supply chains are also more vulnerable to external pressures.
The conflict in Ukraine has seen the price of nickel soar, almost doubling the cost of an EV battery. Finding alternative supply sources and ramping up extraction can take time, and gives vehicle manufacturers a particular headache, especially if they are tied into a long-term supply agreement. Furthermore, is the new supplier operating a sustainable business? Are any increased costs absorbed or passed on to the customer through higher list prices, potentially impacting EV sales at a critical time for the technology?