Is the automotive industry facing a skills crisis?
13 July 2022
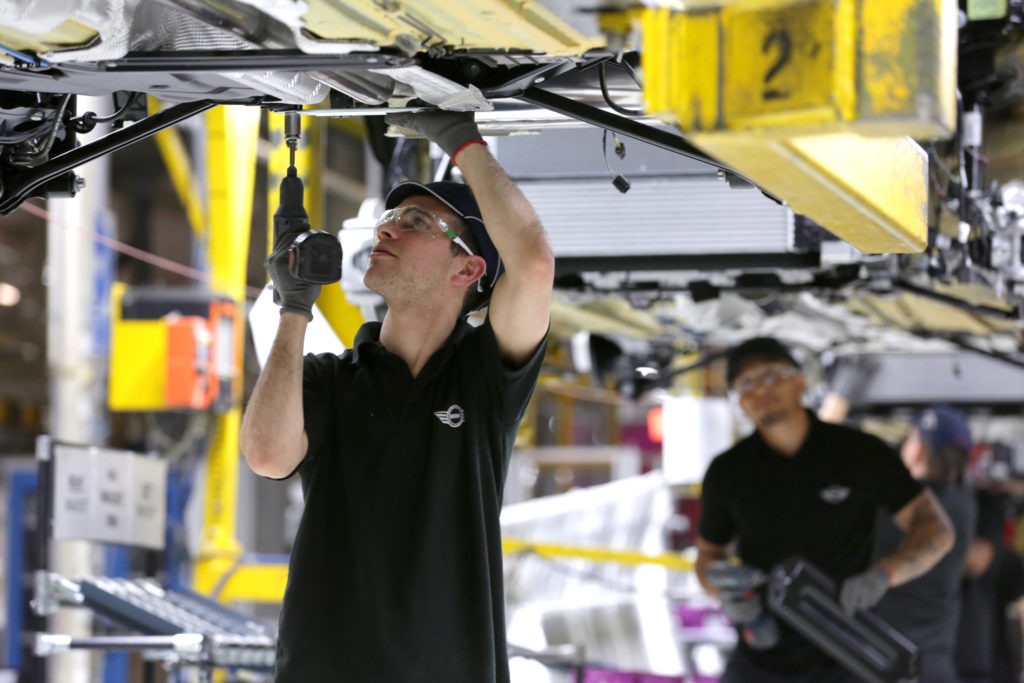
Technology is playing an increasingly important part in today’s automotive industry, but the market relies more on people than anything else. There is a concern that new technologies may lead to job losses while finding the right people for the vacancies is becoming increasingly difficult. Autovista24 editor Phil Curry and deputy editor Tom Geggus discuss the automotive skills crisis.
Subscribe to the Autovista24 podcast and listen to previous episodes on Apple, Spotify, Google Podcasts and Amazon Music.
Show notes
Autovista24 – Energy costs and skills shortages hamper UK automotive industry
SMMT – Report: From full throttle to full charge
Autovista24 – Regional job losses likely as carmakers pick sites for EV production
Reuters – Tesla closes an office as layoff hits autopilot jobs
Reuters – Stellantis unions agree on a further 1,820 voluntary exits in Italy
ACEA – Manufacturing jobs in the EU automotive sector
The IMI – Record-breaking rise in numbers of technicians becoming EV ready
Autovista24 – Thousands of jobs at risk as regulations push for electrification
Bloomberg – Michelin CEO sees mild recession, car market rebound by 2024
Episode synopsis
From vehicle and component manufacturing to sales and repair, a skilled workforce is critical to the success of the automotive industry. But as it changes from a mechanical and engineering-based market to one of electrification and software, are there enough people to meet the new skills demand?
Electrification poses problems when it comes to skills. There is a need to both recruit experts in the new technology, and to train the existing workforce, or risk implementing severe job cuts. At the recent SMMT Automotive Industry Summit, it was highlighted that while an internal-combustion engine requires 10 workers, an electric motor only requires one.
A report commissioned by the body also suggests that the UK possesses few qualified workers who can manufacture battery cells. Yet according to research, by 2025, the country will require 5,000 such workers, rising to 20,000 by 2030. With the banning of the sale of new petrol and diesel vehicles from 2030 in the UK and 2035 in Europe, time is running out to recruit and train the workers required.
Carmakers are also increasingly implementing their own software packages in vehicles. This means they need to recruit in a field that is not only alien to them but also very competitive. In terms of ‘software’, the automotive industry does not instantly spring to mind. Therefore, companies need to focus their recruitment, and one way of doing this is to reach out to schools, colleges, and universities, looking to train the next generation of vehicle developers and hone their skills explicitly for the automotive industry.
Carmakers are reviewing staffing, offering up redundancy packages and carrying out layoffs. Reuters recently reported that Rivian would be briefing employees about potential job losses, while also pausing some programmes as part of a restructuring effort. Elsewhere, Tesla is expected to close its offices in San Mateo, California, laying off 229 workers.
But this is only the tip of the redundancy iceberg, with carmakers like Ford also facing difficult employment decisions. The company has selected a plant in Valencia to manufacture the next generation of its electric vehicles (EVs). While this is good news for the Spanish site, it looks to be a bad outcome for the factory in Saarlouis, Germany, which employs around 4,600 people. Meanwhile, Stellantis and workers’ unions have agreed to cut up to 1,820 positions from the carmaker’s Italian operations through voluntary redundancies.
These ongoing layoffs highlight concerns voiced by the European Association of Automotive Suppliers (CLEPA) last year. The association stated that electrification could cost the industry around 275,000 jobs, even as new employment opportunities are created by EVs. However, it is important to recognise the sector is undergoing a particularly turbulent period, with not all losses attributable to electromobility. Inflation is rising and geopolitical tensions are high and supply-chain issues continue to jeopardise manufacturing.
Skills and knowledge are not just limited to vehicle manufacturing. Workers in dealerships will need to understand more about software and technology in order to connect with customers. The aftermarket repair sector also needs to be aware, yet training in this market is weak.
In the UK, 13% of technicians are EV-ready, according to the Institute of the Motor Industry, which suggests the entire automotive industry has a way to go when it comes to developing the skills needed for the future of mobility.