Sustainable materials are driving change in the automotive industry
09 August 2022
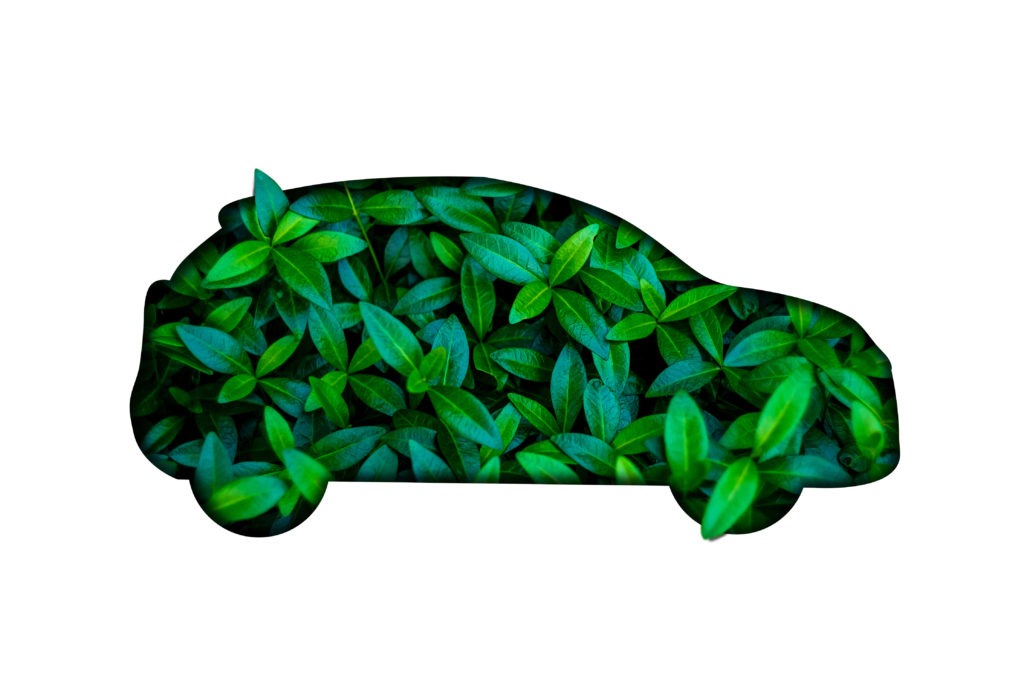
Autovista24 journalist Rebeka Shaid investigates how the use of sustainable materials is transforming the automotive industry.
Cork, coconut fibre, coffee grounds – the automotive industry is moving away from traditional materials that are difficult to recycle. The focus is instead shifting to more sustainable resources. While electromobility is key to slashing carbon emissions, the products that go into a car also matter.
Electrifying powertrains are one way to help decarbonise the lifecycle of a vehicle, but more needs to be done to reduce material emissions. Consulting firm McKinsey estimates that 60% of automotive-industry emissions by 2040 will come from materials used in production, so stepping up decarbonisation efforts in this area is key.
‘Vegan’ leather
Replacing leather with ‘vegan’ alternatives sits at the top of the list for many manufacturers. The idea is not new as carmakers have been using faux or synthetic leather for years. But automotive companies want to take this to the next level by offering greener options. The advantage is that vegan leather can be made from all sorts of natural resources, such as mushrooms or pineapple waste, so the sourcing potential is great.
Swedish carmaker Volvo has vowed to make its electric-vehicle range vegan-friendly by 2030 and other premium manufacturers are eager to explore sustainable leather alternatives as well. BMW is collaborating with Desserto, a company that creates a cactus-based biomaterial, which can replace leather in seats and panels. The material is cruelty-free certified and could help to reduce the environmental impact in product manufacturing, the company said.
The plant-based product, known as Deserttex, promises quality, and the company behind it – Adriano Di Marti – is targeting premium brands to provide them with a product that performs to the expected standards. Luxury automotive brands have taken notice as Dessertex can be found in the upholstery of Mercedes-Benz’s Vision EQXX concept car.
‘The automotive industry is racing into a new world of possibilities around sustainability and mobility — and biotechnology applied to interior materials can significantly contribute,’ Adrian Lopez Velarde, co-founder of Desserto, told Autovista24. ‘In a fast-changing, highly-competitive landscape, Adriano Di Marti is collaborating and innovating with OEMs to accelerate progress on the industry sustainability goals, and we are seeing results.’
Recycled materials
It is not just about vegan leather though, there is also plastic – a material known for its environmental unfriendliness. So how can carmakers make this material more sustainable? Through recycling. Discarded polyethylene terephthalate (PET) bottles or plastic caps have found their way into vehicle interiors, from the dashboard to foam seats and air bags.
Plastic remains a popular material for car manufacturers as it reduces the weight and cost of vehicles while also increasing performance. Around a third of the 30,000 parts used in new vehicles are made from plastic, so recycling the product makes sense from an environmental point of view.
Audi is interested in recycling automotive plastic and last year got involved in a chemical-recycling pilot project in Germany. Considering that on average 250kg of plastic are used in an Audi model, the company sees the re-use of mixed plastic waste as promising.
‘Audi is aware of its responsibility when dealing with resources. This includes the entire lifecycle of a car, from the selection of materials in the design to the materials used in production and the use-phase to the recycling of raw materials. Environmentally friendly materials are already playing a major role in our series models, because a beautiful look and pleasant feel are no longer enough,’ Audi told Autovista24.
The Audi Q4 e-tron boasts a high proportion of recycled materials, comprising up to 27 components that contain recycled material. Meanwhile, floor carpets and mats in the Audi e-tron GT are made from econyl, which consists of up of 100% recycled nylon fibres constructed from production waste or old fishing nets. In the Audi A3, up to 89% of the textile used originates from recycled PET bottles.
While recycling materials can initially be more expensive, this can be compensated for in the long run, Audi added. ‘The most valuable materials are those that can be recycled again and again with little or no loss of quality,’ the company said.
A plastic alternative
Car manufacturers are increasing their decarbonisation efforts with vigour, not least because consumers are demanding more sustainable products. But eco-friendly materials do not only have to be ‘green’, they also need to be appealing to the eye and do their job by being durable.
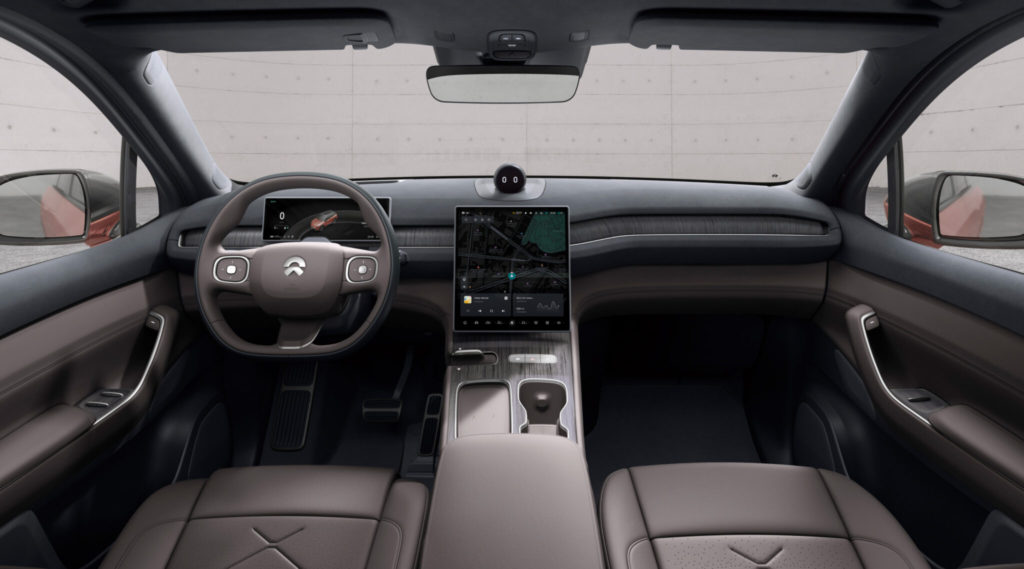
A startup that aims to fulfil these criteria by providing an ecological alternative to plastic is Germany-based Karuun. The company uses rattan, a non-timber product from Indonesia, with the raw material harvested manually before being processed on-site. It has won over notable partners from the automotive industry, including Jaguar Land Rover and Chinese electric-vehicle maker Nio.
‘The quality standards in the automotive industry are among the highest in the industry, meaning that only the best material innovations will be able to be incorporated into a series product,’ Karuun CEO Felix Grüneberger told Autovista24.
‘There is no question that natural materials often require different handling during processing, which may necessitate process adjustments. However, customers can rely on the high quality they are accustomed to from their car brand,’ Grüneberger added.
Saving weight, energy, and emissions
Bio-based materials can also help to minimise weight and increase both energy and emissions savings. The automotive products of green-materials company Bcomp are based on natural-fibre reinforcements for sustainable lightweighting – the concept of reducing vehicle weight to improve performance and efficiency.
Christian Fischer, Bcomp’s CEO, told Autovista24 that sustainable transport is more than electrification. ‘One of the major drivers for sustainability in all transport sectors is lightweighting. Making cars lighter is the most effective way of reducing their energy consumption, regardless of how they are powered,’ he said.
The company has won over notable investors, including BMW, Porsche and Volvo. Its products can cut weight by up to 50% and plastic by 70% in interior panels while also being able to reduce CO2 emissions by 60%. Flax fibres form the base of the components, with the fabrics made from plants in Europe. The fibres can replace plastic, carbon, and glass fibres, which are emissions-intensive to produce.
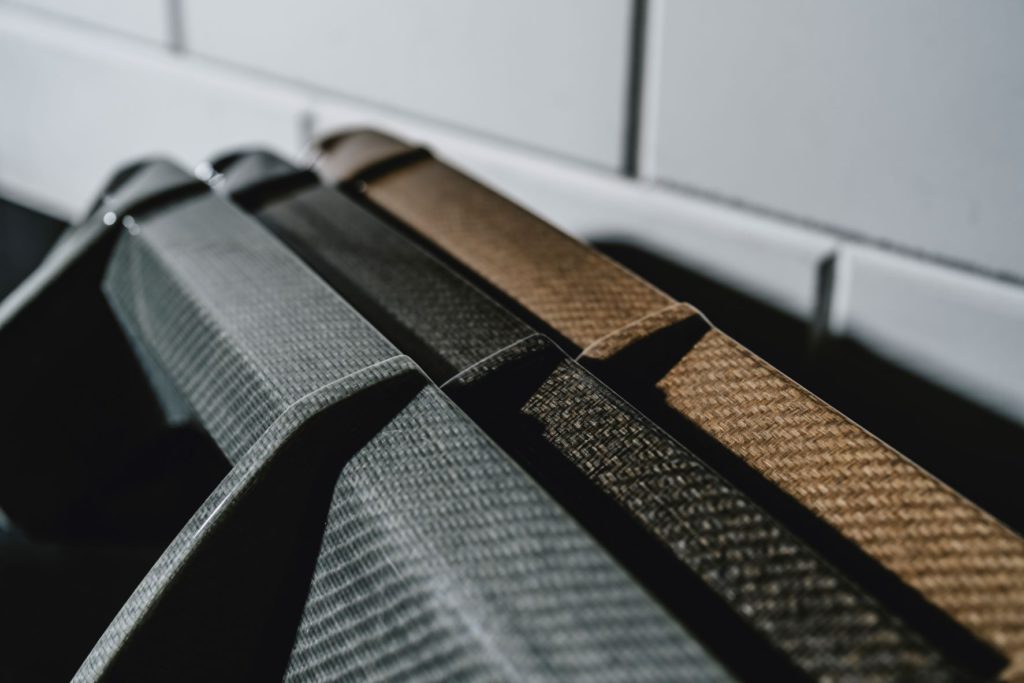
The European Commission recently launched an initiative, known as IRISS, to speed up the transition to sustainably designed materials, products, and processes. CLEPA, the European association of automotive suppliers, joined the three-year project in which the EU is investing more than €3.5 million.
CLEPA’s role is to analyse safe-and-sustainable-by-design criteria, as well as look at research needs and opportunities for implementation in the automotive sector. The association told Autovista24 that Europe’s Green Deal policies are focused on rethinking the way materials are selected, extracted, and incorporated into products.
‘Lightweight materials allow for fuel savings by reducing the vehicle weight but may be more difficult to recycle. So frequently in automotive applications, it is necessary to choose between a resistant and lightweight material and one that is recyclable but with worse technical performance. In practice, the choice is driven by a complex balance between consumer expectations, performance requirements and safety standards, life-cycle analysis, and the increasingly dominant need for circularity. As the concept and scope of sustainability evolves, the balance of trade-off in the automotive industry is shifting, making a clear strategy on sustainable materials a necessity,’ it said.
CLEPA added that the IRISS project would identify the gaps in knowledge and skills for the uptake of a safe-and-sustainable-by-design concept in industrial applications. The focus will also be on materials manufacturing and how these materials behave during the design phase to increase durability.
Carmakers are on their way to carbon neutrality and getting there means building vehicles that rely on greener and sustainably sourced materials that are both renewable and recyclable. With manufacturers working towards on cleaner cars, the path to sustainability remains a challenging one, but sustainable materials can play a big part.
‘Using less material, and materials that are more sustainable is key,’ said Fischer. ‘By 2030, sustainable high-performance materials should be the norm and we are moving away from fossil-based materials wherever possible while also making sure that materials are used, reused, and recycled for as long as possible, and taken care of as efficiently as possible at end of life.’