Green steel – cleaning up a dirty business
15 August 2022
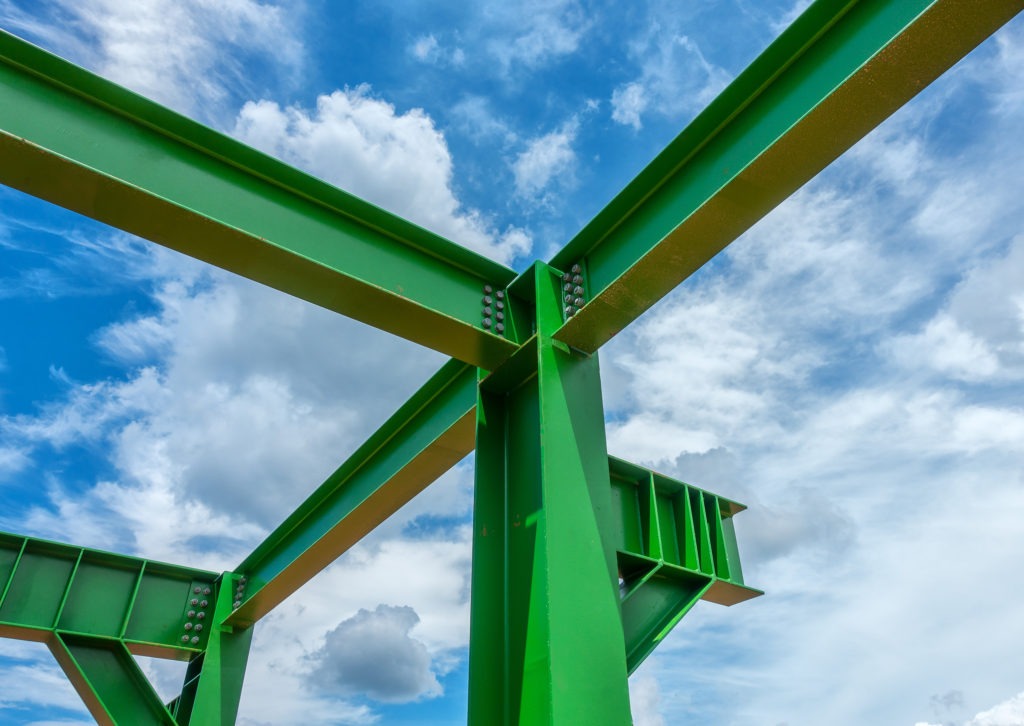
Decarbonising steel remains a challenge, but car and steelmakers are starting to take action, writes Autovista24 journalist Rebeka Shaid.
Steel production is highly polluting, but change might just be around the corner. What has nebulously been branded as ‘green steel’ is turning into a hot commodity in the automotive industry. Both car manufacturers and steelmakers are eager to use and develop more environmentally-friendly steel.
A major contributor to global warming, steelmaking is extremely emissions-intensive and responsible for 7% of carbon-dioxide emissions worldwide. In Europe alone, steel production accounts for 5% of CO2 emissions and a quarter of industrial emissions. But now that companies are on their way to carbon neutrality, attitudes in the industry are starting to shift.
Awareness around sustainability is growing, and new low-carbon technologies are being developed to commercialise ‘greener’ products such as steel. The EU needs to hit vital climate targets in the next decade, pushing suppliers and carmakers to start using lower-emission technology. So, the race is on to source more sustainable materials, including cleaner steel.
What is ‘green’ steel?
In simple terms, green steel is decarbonised steel with the lowest possible level of emissions. The definition is ambiguous and varies from company to company, with common labels including fossil-free, carbon-neutral, and low-carbon steel. Technologies used to produce this type of steel differ and, in many cases, are hydrogen-based.
Germany-based Thyssenkrupp, one of Europe’s largest steelmakers, wants to decarbonise steel, a task that is no easy feat.
‘The question of the cleanliness of green steel, or […] what characterises green steel is currently being defined in the industry associations. Thyssenkrupp Steel does not describe the quantities of steel that are already being produced with lower CO2 emissions as green, but as CO2-reduced,’ the steelmaker told Autovista24.
Thyssenkrupp has partnered with big-oil company BP to make steel ‘greener.’ The company added that the partnership is ‘an important step towards green steel production in the future. In order to reduce carbon emissions, it is in any case necessary to reduce both CO2 emissions of the own process and those of the input materials,’ Thyssenkrupp said.
The company’s steel accounts for almost 3% of CO2 emissions in Germany, and coal-fired blast furnaces are the main culprits. The company is planning to replace these with direct reduction plants, saying that low-carbon energy and hydrogen will play a critical role in achieving decarbonisation. The key is to substitute coking coal with fossil-free electricity and hydrogen. But steel producers now find themselves in the middle of assessing often costly technologies to reduce carbon emissions.
German steel manufacturer Salzgitter also wants to switch to low-emission technologies in the next decade and is aiming to gradually replace blast furnaces and converters. The company has signed deals with German carmakers including Volkswagen Group and BMW, which want to obtain low-carbon steel from 2025, in an endeavour that is supported by the SteelZero initiative.
Fossil-free steel by 2050
To get more businesses involved in both sourcing and using cleaner steel, an initiative was launched by the not-for-profit organisation the Climate Group, which aims to accelerate the switch to a net-zero steel industry.
The group has partnered with ResponsibleSteel, whose automotive members include BMW, Mercedes-Benz, and Volvo Cars. The common goal is to make companies commit to procuring or stocking 100% net-zero steel by 2050. Membership is growing and Volvo was the first car manufacturer to join the SteelZero initiative, vowing to source 100% fossil-free steel by the middle of the century.
‘We know that 12% of the crude steel developed worldwide in 2020 was destined for the transport sector,’ Jen Carson, head of industry at the Climate Group, told Autovista24. ‘This means that a commitment from an automotive manufacturer, like Volvo Cars, sets a significant precedent and challenge to the wider industry.’
The initiative recently set out several policy principles, calling on governments to adopt them and support the steel industry’s decarbonisation. ‘We worked with our corporate members and leading industry policy experts, in the design of these policy principles,’ said Carson. ‘There is not a one-size-fits-all solution, but our six policy principles highlight the action that can be taken now to decarbonise steel.’
The group is asking policymakers to align the steel industry on what is defined as low emission, near-zero, and net-zero steel. Carson pointed out that there is still confusion about what these terms mean, something that ‘holds back progress and hinders collective action on decarbonisation.’
There are other frameworks the group also wants governments to adopt alongside developing standards into public procurement of steel, helping steelmakers transition to new and existing net-zero technologies, maximising the efficient use and recycling of steel, driving the value chain to address embodied carbon, and creating a level playing field for net-zero steel in global markets.
‘Given we have less than 10 years to halve global carbon emissions to get the world on track to reach net zero by mid-century, decarbonising steelmaking needs to be a critical part of the journey. We have to start today,’ said Carson.
Reforming the steel industry
Steel production is indeed starting to change, with seven out of the 10 biggest steel-producing countries having launched at least one green steel project. European steelmakers in particular have recognised the need to rethink their manufacturing strategies, and startups are eager to stir up the market.
Stockholm-based H2 Green Steel is one of those young companies ready to transform the industry. The Swedish firm plans to produce cleaner steel from 2025 by using electricity from fossil-free sources. Instead of relying on coal, it bets on green hydrogen during the manufacturing process.
The company has seen demand for green steel grow quickly and has pre-sold more than 1.5 million tonnes. While prices for cleaner steel are higher, customers are willing to pay a premium for it, the startup said, highlighting the changing market sentiment.
‘After batteries, steel is the next challenge for the automotive industry to tackle when it comes to transforming their products. The demand is there. The steel industry has to transform more quickly to meet the demand,’ H2 Green Steel told Autovista24.
Mercedes-Benz was the first carmaker to take a stake in H2 Green Steel, with the aim to introduce CO₂-free steel into series production. The Swedish firm is planning to build a large-scale production site in northern Sweden, reaffirming Scandinavia’s image as a hotspot for clean technologies. The company started production on its five-million tonne steel plant in July, describing the event as ‘historic’ since no new steel mills have been built in Europe since the 1970s.
While ‘clean’ steel has created a hype, the International Energy Agency expects hydrogen-based steel production to account for just under 15% of primary steel production globally by 2050. Still, there is no choice but for the industry to clean up its act.